Various automation processes in the industry need control of AC induction motors using AC drives. Presented here is a robust system for switching on/off, varying the speed and direction of rotation of an industrial 3 Phase Induction Motor using VFD and PLC. We use here Delta AC motor drive for its operation.
A simple control panel is wired using an Allen Bradley PLC for demonstration. An extended Intouch wonderware SCADA can be developed also.
An electrical motor is an electromechanical device that converts electrical energy into mechanical energy. In the case of 3-phase AC operation, the most-widely-used motor is the 3 Phase Induction Motor as this type of motor does not require any starting device, being a self-starting motor.


What drives are
Often in the industry, need arises for controlling the speed of a 3 Phase Induction Motor. Delta’s AC motor drives are able to efficiently control motor speed, improve machine automation and save energy. Each drive in its variable frequency drive (VFD) series is designed to meet specific application needs.
AC drives accurately control torque, smoothly handle increased load and provide numerous custom control and configuration operating modes. A VFD can be used to vary speed, direction and other parameters of a 3-phase motor. We use the 2-wire method for controlling the speed and direction of the motor.
Working of a VFD
The first stage of a VFD is the converter, which comprises six diodes, which are similar to check valves used in plumbing systems. These allow current to flow in only one direction; the direction shown by the arrow in the diode symbol. For example, whenever A-phase voltage (voltage is similar to pressure in plumbing systems) is more positive than B- or C-phase voltages, that diode opens and allows current to flow.
When B phase becomes more positive than A phase, B-phase diode opens and A-phase diode closes. The same is true for the three diodes on the negative side of the bus. Thus, we get six current pulses as each diode opens and closes. This is called a 6-pulse VFD, which is the standard configuration for current VFDs.
We can get rid of AC ripple on DC bus by adding a capacitor. A capacitor operates in a similar fashion to a reservoir or accumulator in a plumbing system. It absorbs AC ripple and delivers smooth DC voltage.
The diode bridge converter that converts AC to DC is sometimes just referred to as a converter. The converter that converts DC back to AC is also a converter, but to distinguish it from the diode converter, it is usually referred to as an inverter. It has become common in the industry to refer to any DC-to-AC converter as an inverter.
When we close one of the top switches in the inverter, that phase of the motor is connected to the positive DC bus and voltage on that phase becomes positive. When we close one of the bottom switches in the converter, that phase is connected to the negative DC bus and becomes negative. Thus, we can make any phase on the motor positive or negative at will and can thus generate any frequency that we want. So we can make any phase positive, negative or zero.
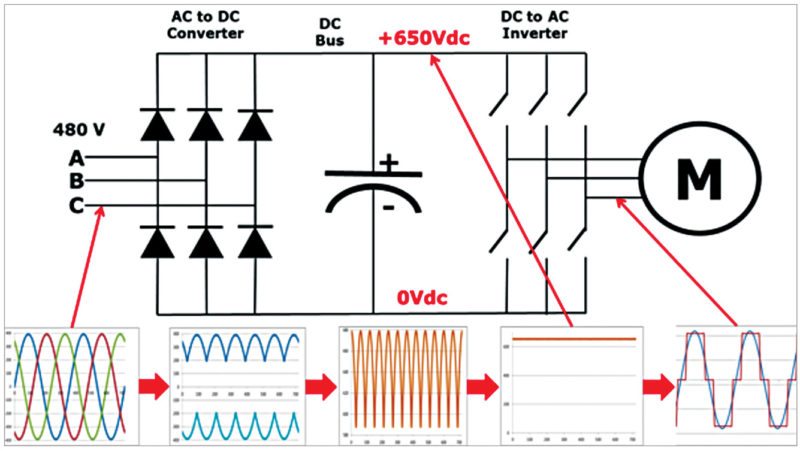
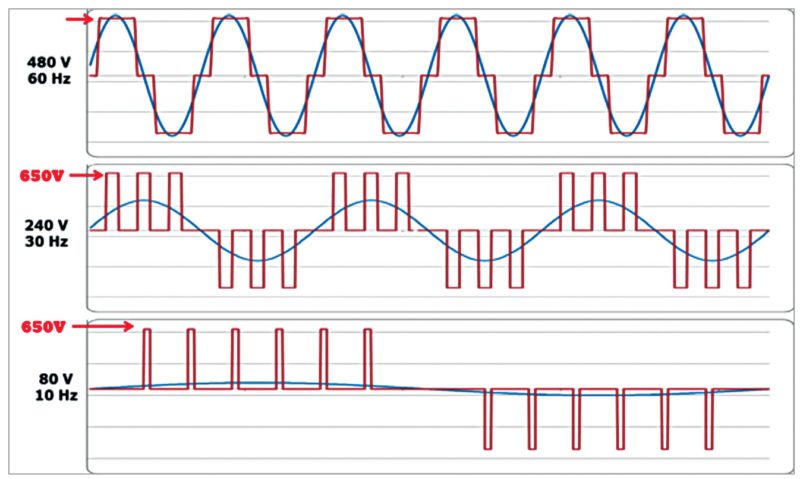
Notice that, the output from the VFD is a rectangular waveform. VFDs do not produce a sinusoidal output. This rectangular waveform would not be a good choice for a general-purpose distribution system, but is perfectly adequate for a motor.
If we want to reduce motor frequency, we simply switch the inverter output transistors more slowly. But if we reduce frequency, we must also reduce voltage in order to maintain V/Hz ratio. Pulse width modulation (PWM) does this.
Imagine, we could control the pressure in a water line by turning the valve on and off at high speed. While this would not be practical for plumbing systems, it works very well for VFDs.
Notice that, during the first half-cycle, voltage is on half the time and off the rest. Thus, the average voltage is half of 480V, that is, 240V. By pulsing the output, we can achieve any average voltage on the output of the VFD.
Selection of Delta VFD-M as AC drive

Delta VFD-M is a sensor-less vector micro AC drive. Its compact design is ideal for small- and medium-horsepower applications. M drive is designed to provide an ultra-low-noise operation and includes several innovative technologies that reduce interference.
This drive can have numerous applications like a packing machine, dumpling machine, treadmill, temperature/humidity-control fan for agriculture and aquaculture, mixer for food processing, grinding machine, drilling machine, small-size hydraulic lathe, elevator, coating equipment, small-size milling machine, robot arm of an injection machine (clamp), wood machine (two-side woodworking planer), edge-bending machine, elasticiser and so on.

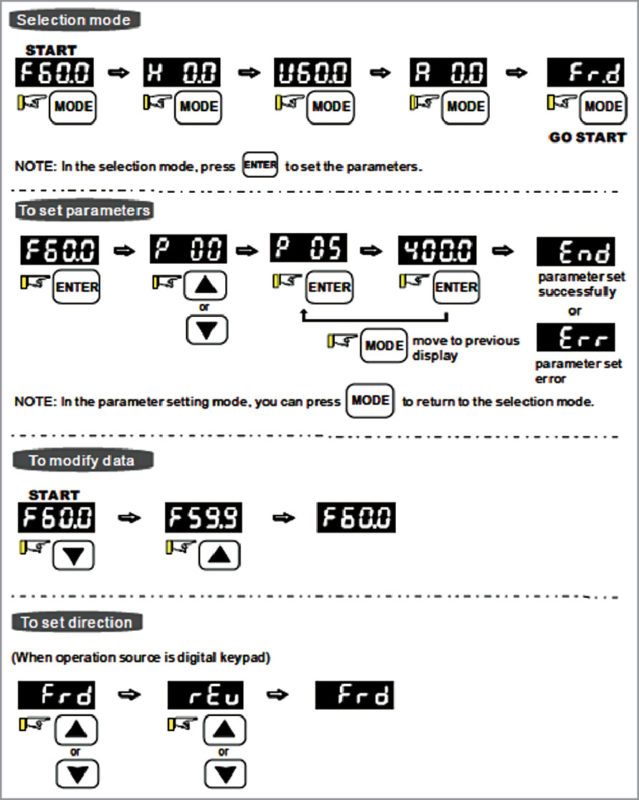
Steps for complete motor control
- Check connections of L1, L2, L3; T1, T2, T3 (used for giving 3-phase input to VFD and connecting motor to it) and wires coming out of M0, M1 and GND.
- Switch on the 3- phase power supply.
- For programming the VFD-M:
(i) Press Mode
(ii) On F60.0, press Enter
(iii) Click Mode
(iv) Select the appropriate parameter using Up/Down keys available on the keypad.
(v) For example, for Pr0, select P 00.
(vi) According to the manual, set the parameters for required mode of operation
(vii) Press EnterEnd
Note: At any point, press Mode to go to the previous step.
For motor running from external controls, we have three modes of operation; two are 2-wire method and one is 3-wire method. Other than these, there is the default method operable from the digital keypad.
First, carry out a trial run to check all connections.
Test run for VFD
The factory setting of the operation source is from the digital keypad (Pr.01=00). You can perform a trial run by using the digital keypad with the following steps:
- After applying power, verify that the display shows F60.0Hz. When AC motor drive is in standby, STOP LED and FWD LED will light up.
- Press down key to set frequency to 5Hz.
- Press run key. RUN LED and FWD LED will light up, which indicates operation command is forward running. And if you want to change to reverse running, you should press down key. And if you want to decelerate to stop, please press stop/reset key.
VFD-M programming
There are two contacts, M0 and M1. Whenever M0 is closed, VFD goes into run mode. If it is open, there is no rotation of the motor. M1 decides the direction of rotation. If M1 is open, it rotates in forward direction; if closed, in reverse direction.
Parameters for the above mode are set as:
Pr.00 set to 01 (for controlling master frequency via potentiometer)
Pr.01 set to 01 (external controls, via M0, M1)
Pr.38 set to 01 (M0, M1 set as run/stop and fwd/rev)
Set Pr.00 to 00 for controlling master frequency using the digital keypad, and 01 for controlling via potentiometer attached as shown in first pin connection diagram.
Pr.38 should be set to 01 as shown in above diagrams.
Once all these parameters are set, follow 2-wire mode operational steps for running the motor.
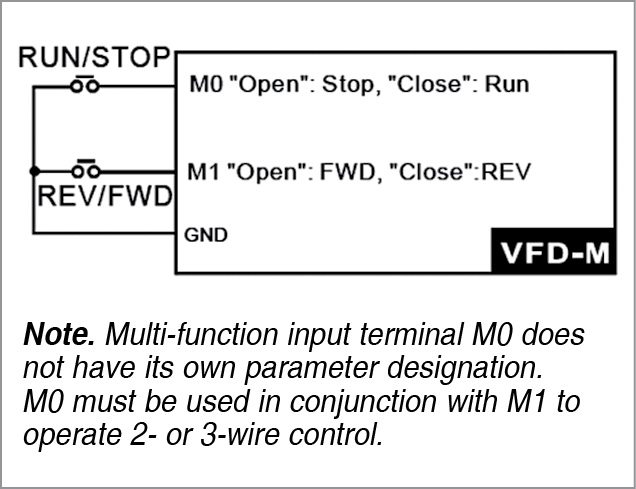
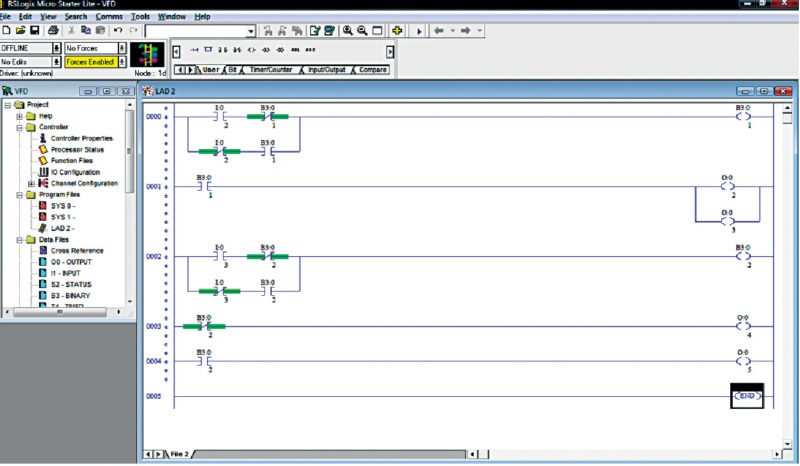
Using the PLC
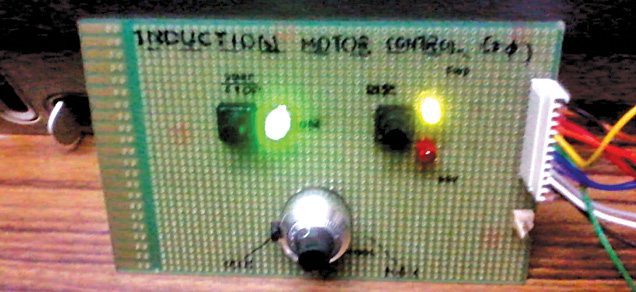
Programmable logic controllers (PLCs) support digital input/output very effectively. So a PLC can also be used to control the operation of a VFD, hence to finally control the connected 3 Phase Induction Motor.

Allen Bradley MicroLogix 1000 PLC is connected to Delta VFD-M and is programmed using Ladder programming using RS Logix.
We connected M0 and M1 to O2 and O3 (outputs) of PLC and control O2 and O3 using Ladder Logic. Fig. 4 shows a logic defined for mode 01, that is, Pr.38 = 01. O:0.0/2 is connected to M0.
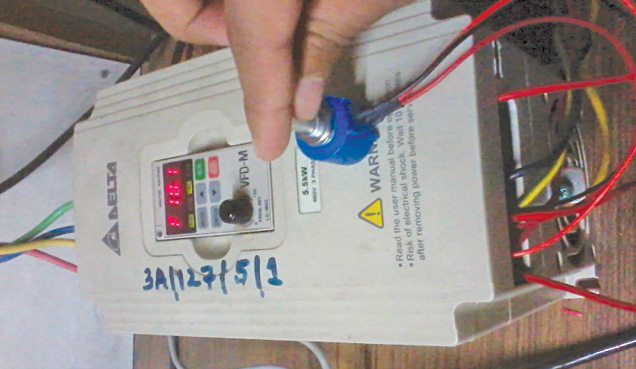
When I:0.0/2 is set on, it puts the motor in run mode. Now, even if I:0.0/2 is switched off, O:0.0/2 remains on due to the logic defined. It can only be stopped by pressing I:0.0/2 again.
I:0.0/3 controls O:0.0/5, which, in turn, is connected to M1, which decides the direction of rotation of the motor.
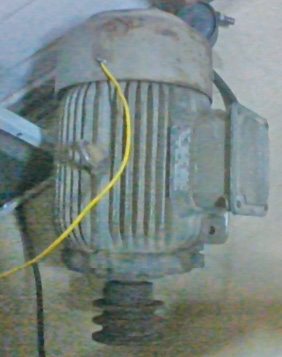
0:0.0/3 is the LED that turns on when the motor is in run mode.
0:0.0/5 is the LED that turns on when the motor is running in forward direction and turns off in reverse rotation.
Love reading this article? You may also like Building a PC Control System Using Wonderware InTouch SCADA and Allen Bradley PLC
Joby Antony is masters in computer technology from the USA, and is currently working as engineer-F at Nuclear Inter-University Accelerator Centre (IUAC), New Delhi. He was also a visiting scientist at CERN, Geneva
Akshay Kumar is a B.Tech student at Delhi Technological University, New Delhi, and currently an intern at IUAC
Wonderful! Could you help me design a circuit for a machine that I am trying to build?
We have several circuit projects. Please check if your machine idea fits into any of these. You can also send us your project idea and we will forward it to the concerned team. You can also discuss your project at our forum page.
Thank you very much for this post..
You are most welcome.
Hello dear i hope you are ok but my problem is that our stepper motor speed does not controlled with omron plc and vfd please can you help me
excellent job very good keep it up
Thank you for your valuable feedback
Anyone,please do help me in providing the logic code which is used here in PLC?
We’re going to build a motor control trainer using VFD and PLC could you please help us and give some ideas.
Kindly elaborate your query.
Comment: how can I know which one is the input and output connection on a three phase vfd if the connection point are not lebled IN and OUT
Hi I love what you have done above in this project. I am currently trying to do something similar controlling 3 phase motor via a vsd with an ABB Plc. I was wondering if it would be possible to download or purchase all of the info you have on this project. I am sure it would be of great benefit to me. Thank you in advance for your help
I have aproblem with three phase induction motor (132kw) with sinamics 330pm vfd , that the motor produce acoustic noise at 2khz and speed875rpm
But no noise at 4khz at speed 860rpm
Sir which based to know selection of VFD in AHU given of Motor Speed And Fan Speed
Sir plz help me….How to maintain the constant speed of “Induction Motor” while varying load.
will anybody be able to help me to make my roll foaming machine auto measure the length of sheets,auto cutting using PLC systems for motor, senser etc complete as I have seen on YouTube the operation of such machine is automatic.please give me complete details.
So far all electric vehicles use a low voltage high amps ac / dc motor. But I with to use a 220v 5hp ac motor with a VFD and a foot throttle to convert my regular car to electric?
1. 48v 100ah lifepo4 batteries connected to a 5 kva inverter.
2. Output from the inverter is provided to the VFD.
3. VFD provides power to the motor and with the use of a throttle speed of the motor can be adjusted as per requirement.
I need assistance to get this sorted.
Thank you in advance
Punit
5HP? Are you sure about this? That’s the same power as a small motorcycle. What is the rated power output of your car?
Im from Colombia Mr Punit Patel. We are converting a car in this moments. We need make a team to develop the same project. Its OK? My name is Alfonso Campos from Barranquilla, Colombia South America. My team star the last month this project with my old car Chevrolet Chevette model 1985. We have photos and all data of this car. We are development in thso moments the driver and power module in Proteus and arduino. If like add to thos team olease add my whatss app 57+3165197978 or write me to alfonsocamposdelosreyes@gmail or [email protected] Thanks Mr Punit
I am looking for a custom 3 Phase Motor Controller.
I am working on a type of propulsion system which is working with High Voltage and High frequency.
What we are sending in this motor is High Voltage at the resonant frequency of the magnets.
I need a 3 Phase Motor Controller with
Adjustable High Voltage ca. 1500 V and with adjustable High Frequency up to 1500 Hz.
Can You help me with this.
Looking forward to Your reply.
Greetings, Sandor contact email: [email protected]
i am looking matlab code for speed control of induction motor using vfd help me