Capacitors are common passive elements in all electronic devices, including vehicles. The usage of capacitors in vehicles is expected to increase in the coming years as electric vehicles (EVs) gain popularity. It is important to select capacitors wisely in order to combat common issues that occur in vehicular circuitry
Vehicular systems today have become vastly advanced. Smart cars, self-driving cars, electric vehicles, etc are rapidly gaining popularity not only among the wealthy but also among the middle-class society. Thanks to the huge boom of innovation in this field, there is a need for better and more durable electronic components, both passive and active.
Capacitors are widely used in the automotive industry. In fact, they are crucial to the functioning of a vehicle. They provide stability and are used in the management of current in the vehicle’s circuitry. They are also used to ensure that the design is free from interference. Capacitors play a major role in braking systems, window wipers, seat aligners, airbag controllers, and many other important applications inside a vehicle.
Capacitors in EVs
Driven by concerns about petrol prices, government environmental initiatives, and large-scale public and private investment in the supporting charging infrastructure, the electric vehicle (EV) sector is undergoing a period of substantial growth. Over the course of the next decade, the automotive market is set to transition from being dominated by internal combustion engine (ICE) vehicles to one where EVs make up the majority of new vehicle sales.
ICE vehicles have relied on 12V and 24V powertrain architectures, with hybrids often being based on 48V systems. EVs, however, have powertrains that are placed at far higher voltages. Further, in order to accelerate charge times and increase conversion efficiencies, the voltages are being pushed even higher. The new EV models that are just starting to appear on the market have 800V powertrain ratings!
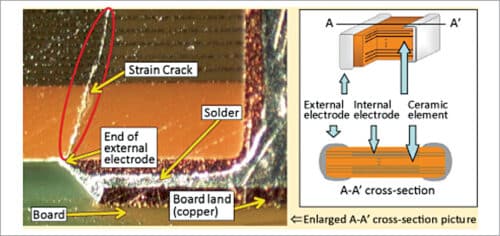
For the first time, worldwide EV annual sales surpassed 6 million units in 2021. Predictions made by the International Energy Agency (IEA) suggest that this is just the beginning. It forecasts that sales will have reached 15 million by 2025 and 25 million by 2030. The powertrains of EVs need to support higher voltage levels compared to their ICE counterparts, and this will have major implications when it comes to specifying constituent passive components.
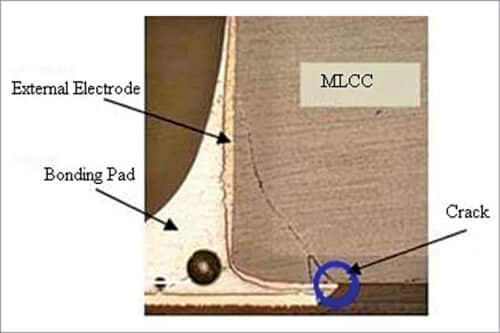
Even for 48V hybrid systems, the motors will be located on the powertrain itself. This does, however, mean that the accompanying electronics will be exposed to more intense vibrations and thermal cycling. Factors like vibrations, shock, and stress have clear effects on the passive components present in the system. Therefore, automotive engineers must look at the effects this will have on component reliability.
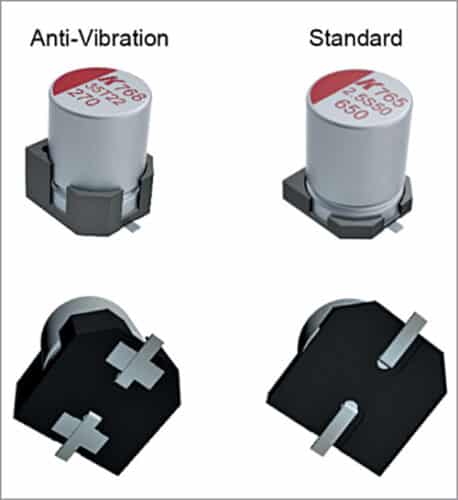
ESR: An important parameter
A key performance parameter for any DC-Link capacitor will be its equivalent series resistance (ESR) value. The lower the ESR of a capacitor, the greater its ability to smooth out high-frequency voltage disturbances passing through the powertrain. If the ESR values that these capacitors present within the electrical circuitry increase due to some form of damage, the whole powertrain operation could potentially be jeopardised.
While selecting capacitors that conform to these factors, vehicle manufacturers must keep the overall bill-of-materials expense as low as possible, so the chosen capacitors have to be cost-effective. There is, therefore, a constant tradeoff between efficiency and cost, and engineers need to maintain both sides of the equation for the vehicle to be optimal.
Please register to view this article or log in below.