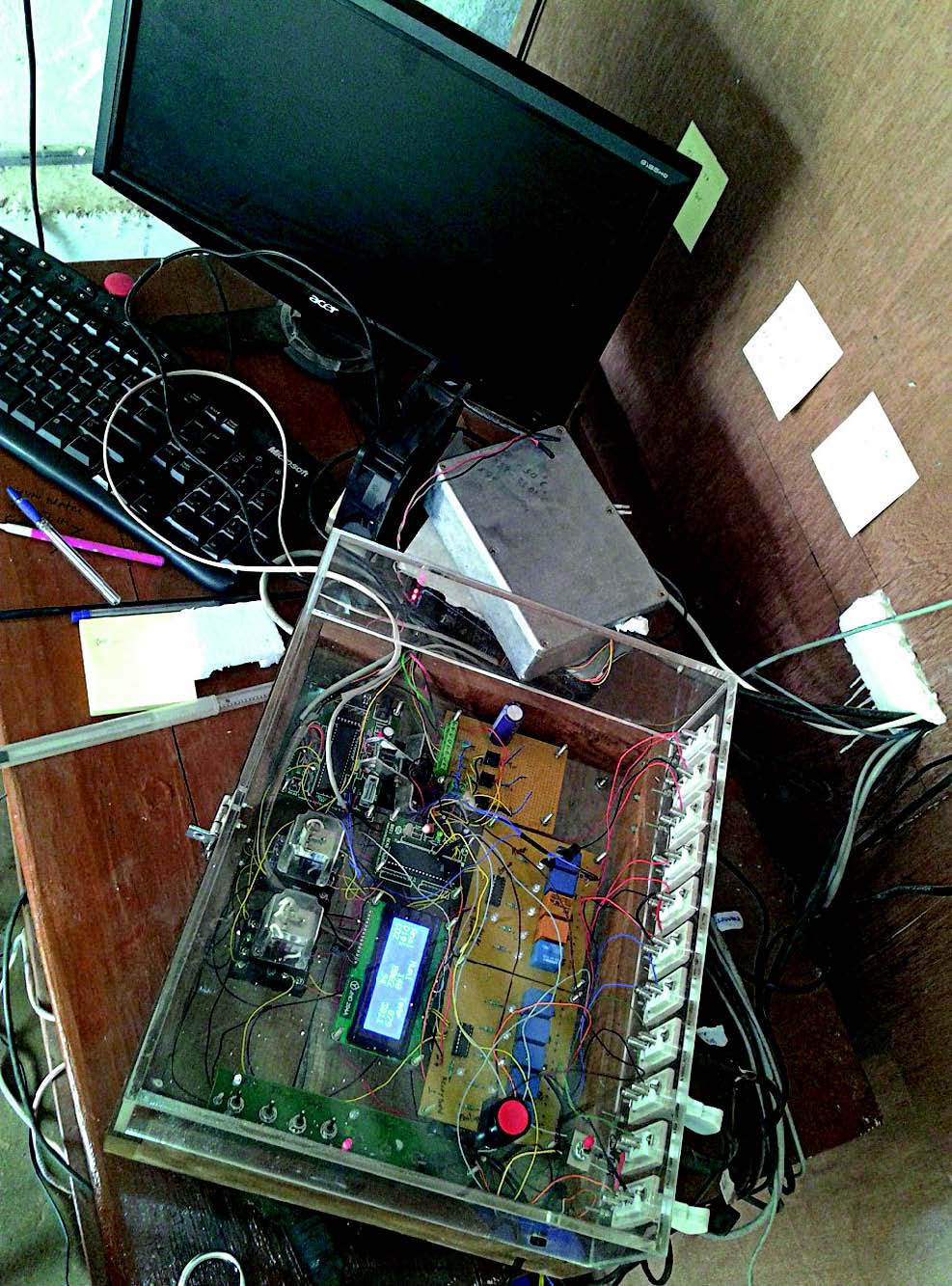
Poultry incubators need a constant source of power to maintain optimal temperature, humidity and other parameters for successful egg hatching. However, In India, power failures are a major headache for the poultry farmers. Some of them have diesel generators to offset the effect, but this drives the cost of eggs up and small-scale farmers get affected the most.
Karthik K.G. and Sakthi Prakash P., managing partners at Pluto India, have come up with an automated battery-run poultry incubator to counter this problem.
[stextbox id=”info” caption=”What’s an incubator”]
An incubator is a device that simulates avian incubation by keeping eggs warm and at the correct humidity, to hatch them. Modern incubators are electrically heated with a thermostat.
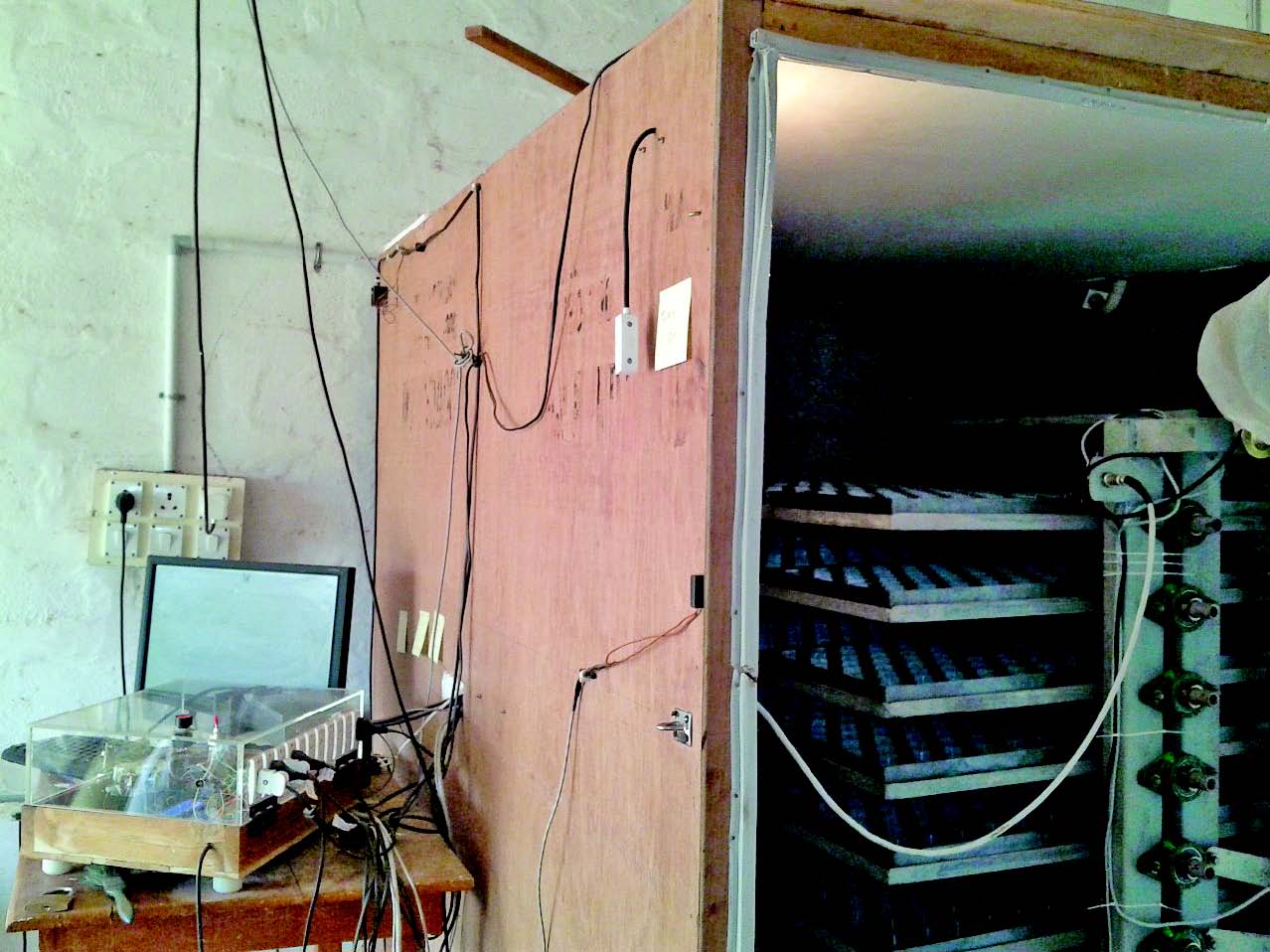
The incubator maintains optimal temperature, humidity and air quality (CO2) inside in the total 21 days of incubation. In the first 18 days, eggs are placed in a chamber called ‘setter.’ Here the eggs need to be tilted frequently during the day in order to avoid chicks getting stuck to the egg shell. During the remaining three days, they are kept in a chamber called ‘hatcher.’
Whenever the CO2 level inside the chamber reaches an alarming value, the exhaust fan runs to fill the chamber with fresh air. To maintain temperature and humidity, a heater and an ultrasonic humidifier, respectively, are used.
[/stextbox]
The solution
The battery-run incubator developed by Karthik and Sakthi uses a 150Ah battery and inverter set-up. While designing a power-efficient solution at every level, they have also ensured the quality of egg hatching. During the first week, they had a pretty low mortality rate for the chicks.
The system is automated, sensing all the parameters associated with a control cycle and logging their status onto a computer. This data includes incubator/hatcher door status, sensor-1 humidity, sensor-2 humidity (redundancy), sensor-1 temperature, sensor-2 temperature (redundancy), CO2 level, tray tilting status, heater status, humidifier status and exhaust fan status.
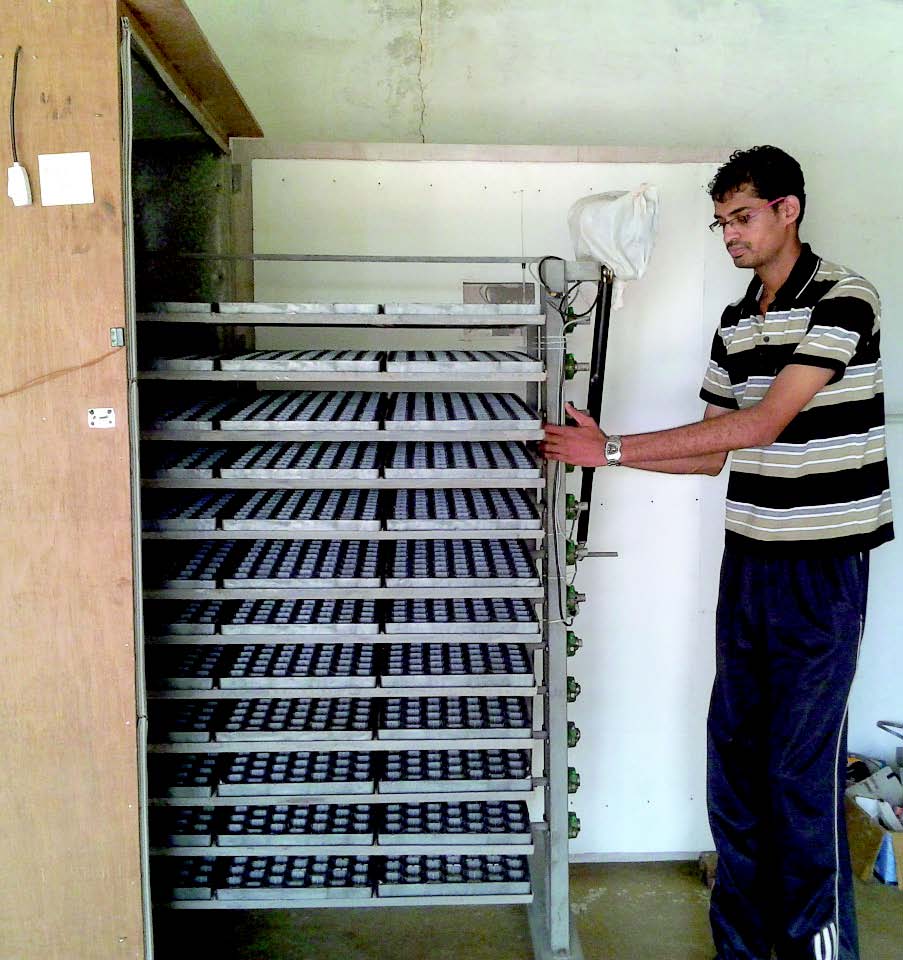
The logged data is graphically presented on a computer. In case of emergency, the requisite set of notifications is sent to the respective people.
Sakthi explains, “This system works by efficiently utilising a pre-charged battery’s energy, rather than requiring a separate power generator. We have designed electronic measurement and control systems that assist in efficient use of the battery heater. This heater gives the same amount of power as a mains-powered heater would. A typical mains-powered heater operates off 230V AC supply, but a battery heater has to work from 12V DC supply. Hence the heater is designed using a suitable heating element that works off 12V DC supply. To avoid the use of an always-open vent (required to maintain air quality) as in commercial incubators, air quality is monitored to ensure that the vent is open only when required. This is again a big power saver.”
Challenges
Karthik informs that the challenges were mainly three-fold: One related to the relative humidity measurement system, another concerning the battery heater and the third dealing with the mechanical system for the incubator.
Relative humidity. An IC-based sensor was initially used to measure the relative humidity. But it lacked robustness and reliability. The electronics embedded along with the sensing capacitive element was later found to be affected by the outside changing conditions.
To avoid the above problem, the electronics was separated from the capacitive element by a coaxial cable. The coaxial cable introduced a new problem of change in its capacitance when the cable was bent for routing. The change in capacitance was very huge compared to small capacitive changes of the sensing element. As bending the cable for routing was unavoidable, the circuit had to be re-designed to suppress the capacitance of the coaxial cable. The circuit was designed and checked for reliability under extreme conditions. Humidity control is achieved by using an ultrasonic humidifier.
Battery heater. To maintain optimal temperature during power cut, the heater is designed to tap the stored electrical energy from the battery in the most efficient way possible. To convert the maximum-possible electrical energy stored in the battery into heat in the incubator, the heater is made to operate off 12V DC rather than 230V AC or 110V AC, which is the usual supply.
Karthik adds, “If we had to use a 230V AC heater even during power cut, it would have required conversion of 12V DC from the battery into 230V AC. Since the inverter efficiency is typically 50 per cent, the method of inverting to AC voltage for heater usage is an inefficient way. Hence a heater had to be designed that worked off 12V DC to avoid wastage of energy.”