Electric vehicles (EVs), Industry 4.0, and AI/ML are some of the buzzwords that we hear quite frequently today. With more and more industries leveraging new-age technologies like the Internet of Things (IoT) and artificial intelligence (AI), it is only fair that the automotive industry should also hop on the ride. Amalgamating these buzzwords to bring out semblance in the EV manufacturing process is becoming a key driver for the growth of the EV industry
EVs are being talked about more and more in the context of mobility, energy, and connectivity where every aspect is complementing the other. There is more chatter around Industry 4.0, where all technologies are getting integrated in a way that it becomes a whole ‘energy universe’ and automobiles are a part of that universe. EV is not just a transportation device anymore; it is a part of the whole energy ecosystem.
As such, leveraging digital technology to add value to the EV production processes is the obvious choice for any OEM. There is an opportunity for most citizens of the world to become prosumers and actively participate in the transition to cleaner energy for mobility and electricity.
“I think digitalisation is something that we are going to see more and more, right from the product development to product approval, manufacturing and then managing the customer, or forward linkage when the product goes to the market. So, my opinion is that there is a huge scope of using various technologies like simulation, data analytics, and AI/ML, and bringing them all together in the technology stack, and this is like the foundation of a building. It will govern all the links of the supply-chain,” says Deb Mukherjee, Managing Director, Omega Seiki Mobility.
Leveraging Digitalisation For Product Development
“When we talk about digitalisation in product design, process design, manufacturing engineering etc, even in the era of ICE engines these tools used to be there. We did the designs using CAD and simulation tools that were there,” says Mukherjee.
In the context of EV, however, product-specific digitalisation becomes important because it calls for certain specific design capabilities and simulation. Especially in terms of simulation, there are two specific requirements—accuracy of the simulation and reducing product development time. Simulation tools are being leveraged extensively by successful EV giants like Tesla, who have brought down the product lead time significantly with the increased accuracy in simulation.
Simulation For Increased Efficiency
Digital tools have also helped in the development of the components of EVs—particularly the ones like battery, motor, charging device, and DC-DC converter, where the development time is reduced by one-fourth and the cost is also optimised because the team knows where it is moving to. Virtual simulation has been a boon to the industry, especially in terms of the number of iterations that can be made during the product development process, while also being cost-efficient.
“With miniaturisation of systems in virtual simulation, you can enhance the scope of the passenger compartment, if you want, since you can miniaturise it and place it anywhere. This is possible in the digital approach. How many models will you build if you are to adopt the traditional approach? It would also be extremely costly,” explains Samir Kumar Mishra, CTO, JBM Group.
The same can be seen with the digital twin approach where the product will be running in real time along with a twin system in the cloud space. Anytime there is a problem, we can test back to the component level. This is also thanks to the introduction of AI, which allows us to predict certain elements without having to make the product go through them. Anytime a problem arises, it can be simulated artificially, pre-programmed, and there is auto-dynamistic mode by default where some similar problems can be seen based on the prevailing environment. That gives enough hints of the problems that could occur.
M.A. Patwardhan, GM-Engineering Design & Simulation, ARAI, notes, “My opinion is that EVs are a better candidate for the digital factories compared to the traditional factories since Industry 4.0 and other kinds of tools can be employed for a digital factory.”
The main purpose of the digital factory is to validate and optimise the design of different production plans in virtual form during the planning phase itself. This can be seamlessly done through the integration of 3D simulation tools and visualisation tools, radically transforming the industry and production value chain for EVs.
Product Design
Diving a little deeper on the design side, the introduction of digitalisation into the product lifecycle management (PLM), where it is equipped with the latest simulation tools, has been a boon. In traditional architecture of the gasoline vehicle, the vehicle is designed around one or two components that are central to the product but become a constraint. When someone wants to replace those components, it becomes difficult to go back to the design and change them. It takes a complete iteration process to do that.
With the digitisation in PLM, it becomes a plug-and-play kind of system where we can just change a couple of components and work around the design right from the beginning with five to six components. Thus, there is not much of a risk in the supply-chain when there is a constraint to a component around which the vehicle production is running. The things are already fitted and plugged and played, and any additional components can be included in the design. This is the power of the PLM.
Another aspect in designing, which has been carried over from the traditional approach, is called ‘Class of Titans’ where two titans—the car designer or stylist and the engineering team—do not see eye to eye at any time. There is always a clash in the traditional design approach because the two do not sit together and work hand in hand. This issue disappears with virtual simulation as there is now a platform for them to work remotely and yet coordinate with each other, thus enhancing the time to market and quality of the product.
Digitalisation In Battery Management
Batteries are one of the most important aspects of EV. As such, battery development and management need to be efficient, which is possible through digitalisation. Battery development includes processes such as thermal simulation, battery behaviour, battery life management, and charging.
“There is an opportunity for more democratisation of energy where both the manufacturing side as well as the generation and management of the consumption of energy can be better monitored through digitalisation,” explains Bharath Krishna Rao, Managing Director, Emobi Manufacturing Ltd.
Machine learning (ML) is another critical digital aspect that can be leveraged by the EV industry, especially in terms of battery packs where there is huge field case data. This data can be used to train the process and devise a system through ML for certain eventualities and the possible responses.
Similarly, tracing and tracking the battery cells all through their life-cycle to assess their behaviour in different climatic conditions and see their performance in different pack configurations, and different form factors for different vehicle level applications, also provides crucial data. Pulling all that data into a common platform, AI/ML algorithms can be used to determine important parameters that set the tone for better battery chemistries to be developed in the future.
This data also helps in integrating other components of the EV, such as controllers and vehicle management systems, to communicate and work along with the battery by exchanging crucial data points. “This will allow us to expand at a larger and faster pace to make more microfactories viable, where the core elements of the vehicle management system can be consolidated by core OEMs, while you can have several assembly partners who could help increase the pace of deployment of EVs into global markets. This is only possible with really integrating with digitalisation right from the suppliers’ facility all the way to the consumer’s hand and back from the consumer for second-life use case based on the state of the battery or being used for recycling based on the state of the battery,” adds Rao.
Boosting Charging Infrastructure
With digitalisation comes globalisation as it becomes easy to communicate with different factories around the world through integrated IT platforms run on IoT and cloud. The digitalisation at global level helps not only in the charging infrastructure, it is also used in selecting the right energy supplier and buying and selling energy.
The charging infrastructure, for one, can be boosted tremendously through the right shift of data. For instance, in smart charging, whenever a user plugs in an EV, information related to charging speed and time, the charge-point usage pattern, and the grid capacity can be sent to the cloud and analysed in real time to gain insights to manage the grid capacity.
Innovations like wireless charging, which India is yet to catch up with, also demand use of digital tools to their full potential.
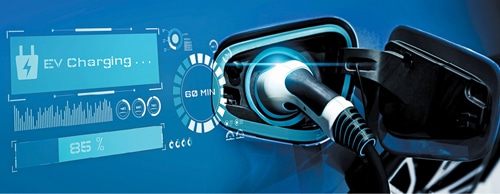
Challenges In Digitalisation
It is common among EV OEMs in the two- and three-wheeler segments to follow the retrofit approach, where they retrofit a battery kit into an ICE vehicle and turn it into an EV. The biggest challenge right now is to build an EV from the ground up.
“You have to design the entire thing with a clean chit approach. This is where your knowledge of vehicle engineering, vehicle architecture, and the whole way of packaging it together in the most efficient and safe way is going to be tested, and this is where these technologies will be used,” notes Mukherjee.
Digitalisation ought to help in EV development. Yet, keeping abreast with these technologies can be cumbersome. Batteries, for instance, are constantly evolving with new chemistries and materials being tested every day. Additionally, keeping up with the hardware trends in terms of motors and powertrains is equally important.
“This is where you got to keep up, and this is where technologies like ML/AI will come in handy, wherein huge amounts of data points will come in handy and they can be put together so that you don’t waste time in doing hits and trials,” adds Mukherjee.
Lack Of Data Points
There is more reliance in the EV segment, compared to the ICE, on digital product validation. The reason is that not all EV platforms are time-tested compared to the ICE engines.
If you look at EVs, by and large, the vehicle structure has not changed; instead of ICE powertrain, the EV powertrain has been embedded. So, whatever product development has been happening in the ICE related to structures will remain the same.
But for aspects like battery thermal management and other electronics being tested, there is no time-tested data available for EVs. Therefore simulation and data generation through IoT is even more essential to help innovate in the field.
Standardisation And Academia-Industry Collaboration
“We should not miss the bus of this technological revolution like we did in case of ICE and then semiconductors. We should be more proactive and come up with a big portfolio of indigenous technology,” says Praveen Kumar, Professor at IIT-Guwahati.
But indigenous technology requires standardisation, and standardisation requires research. There is an urgent need for the academia to work on building innovations that are suitable for the Indian context and join hands with the industry to apply them as standards for the entire manufacturing and supply-chain. “We need indigenous research instead of following what other countries are doing and then build EVs that fit the bill,” adds Mishra.
This will lay the groundwork for an application-wise dominion that is fixed right from the design stage, so any product falling into that application is always standardised irrespective of different manufacturers and the supply-chain. This will not only help in cost reduction but also decrease the lead time of the product reaching the market, eventually boosting EV adoption in the country.
The Future Of Manufacturing
We are witnessing an exciting amalgamation of digital with hardware, making it one of the most exciting times for technology and manufacturing, which will have a profound impact over the next decade.
Mukherjee says, “We will see the entire energy mix change, and it is a game where multiple stakeholders will have to come together. I wish I was 25 years younger so I could participate more actively in this revolution!”
It is surely exciting to see how humanity will move away from fossil fuels to a more sustainable means of harnessing renewables and using it for both mobility and energy. With the right combination of working with academic institutions, OEMs, and consumers, which in today’s world is possible with the advent of internet connectivity, EV manufacturing will not only be revolutionised but will propel India to the global table of energy efficiency that it has targeted to meet by 2050.
This article is based on opinions shared by the speakers during public events. Transcribed and curated by EFY’s Siddha Dhar.