You may not have noticed, but modern vehicles are filled with intelligent controllers that are hidden away in small spaces. Even basic or mid-range vehicles there are likely to be around 100 electronic control units (ECUs) fitted and probably more than this in high-end models. The ECUs manage almost all functions of the vehicle including the engine, braking, transmission and climate control.
These ECUs communicate with each other in order to co-ordinate the functions of the vehicle. Currently the communication is over one of several busses, although these protocols and standards will change rapidly to accommodate the need for higher performance and greater responsiveness.
As more features are added and existing features become more data-intensive, so the bandwidth requirements within vehicles have increased significantly. One significant contributor to this trend has been the advanced driver assistance systems (ADAS) that requires the collection and processing of significant amounts of data, including video from multiple cameras. As autonomous driving becomes a reality then the data traffic within vehicles is expected to increase by another order of magnitude.
Existing protocols such as LIN (local interconnect network) and CAN (controller area network) are still used in many vehicles, but their operational limitations are now becoming obvious and they are struggling to cope. Recently introduced protocols such as MOST (media-oriented systems transport) and FlexRay were expected to become the next generation but have only had a limited rollout and not become mainstream.
While many different busses are in place, this fragmented situation is not ideal and many vehicle manufacturers and their tier one suppliers want a more standardized approach to in-vehicle networking. Primary considerations are that any new approach will have faster data rates and lower latency, as well as reducing the amount and weight of cabling, contributing to reduced build costs and greater fuel economy. With the prevalence of various forms of cyberattack, manufacturers and suppliers are also seeing a networking technology that offer a higher degree of operational security.
Ethernet: A potential solution
The automotive industry is starting to see the potential of Ethernet for next-generation in-vehicle networking. This highly popular protocol is used extensively in commercial and industrial areas and increasingly in our homes, meaning that there is a huge base of software and tools available as well as low-cost components that are produced in their millions, available for use in vehicle installations.
In order to promote the use of Ethernet (and other IEEE standards) in vehicles, the One-Pair EtherNet (OPEN) Alliance Special Interest Group (SIG) has been formed by industry leaders including BMW, Broadcom, Freescale, Harman, Hyundai and NXP.
However, vehicles provide a very different environment and there are many considerations that must be accounted for that simply do not exist in fixed installations. To save space and reduce weight, data will be transmitted over a single unshielded twisted pair (UTP) rather than several pairs as used in conventional Ethernet. The vehicle’s environment will have higher temperatures and interference from electro-static discharge (ESD) and electro-magnetic interference (EMI). Notwithstanding the rigors of the environment, data integrity is essential, so the Ethernet PHY transceivers have to be able to ensure an adequate bit error rate (BER) in even the most demanding conditions.
Essential safety-related functionality that relies on the network, such as ADAS will require low-latency and ideally fully deterministic operation, which is not supported by the CSMA/CD operation of normal Ethernet. Undue network delays due to traffic bottlenecks will literally risk the lives of passengers, pedestrians and other road users.
While the vehicle is parked and off, much of the electronics (including the ECUs) will be fully off, but the PHYs will remain partially powered waking the system in the event of network activity. As they will be draining the battery, low power operation is essential. Fortunately, the high levels of integration of modern PHYs means that there are few, if any, external components and generally the level of current drain is very small.
In order to meet the needs of automotive Ethernet, the new 100BASE-T1 (IEEE 802.3bw) protocol was developed. This was specifically intended to meet the elevated data rates needed, achieving 100 Mbps with half-duplex operation as well as reducing latency in the system. Issues such as potential EMI were addressed through techniques such as overlap and specific encoding and scrambling systems.
Looking to the future, 1000BASE-T1 (IEEE 802.3bp) is a full-duplex protocol that is able to achieve speeds of 1 Gbps and it is available now. Further into the future, multi-Gigabit data rates will be required and there is already development work under way to achieve this.
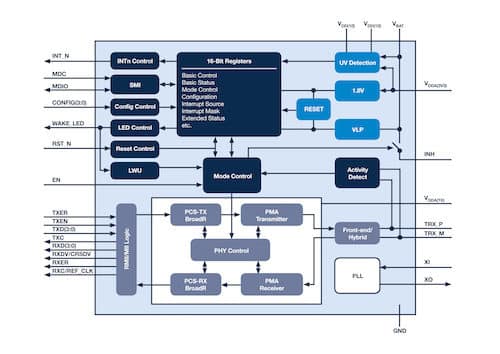
Products for automotive Ethernet
Companies such as NXP, Microchip and Broadcom are actively involved in the development of new standards and also have a wide range of automotive ICs available. NXP’s TJA1100 is a single-port 100BASE-T1 Ethernet PHY with 100Mbps data rates (shown in figure 1). The device operates with a low current draw due to an inbuilt 1.8V LDO voltage regulator and a sleep mode with local wake-up support. The device is ideally suited to automotive applications with a -40C to +125C working temperature range and full AEC-Q100 qualification.
Texas Instruments’ DP83TC811S-Q1 100Mbps Ethernet PHY (see figure 2) is compatible with multiple independent multimedia interfaces and includes a comprehensive diagnostic toolkit to detect issues such as broken cables and ESD strikes as well as temperature and voltage variations.
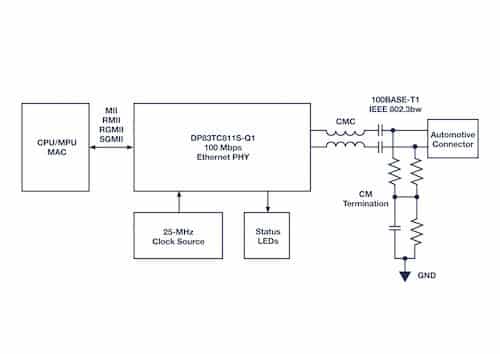
Microchip’s KSZ9031RNX (block diagram in figure 2) is a 10BASE-T/100BASE-TX/1000BASE-T capable Ethernet PHY that has been optimised for modern automotive applications. The device is housed in a 48-pin, lead-free QFN package, and achieves a maximum data rate of 1 Gbps with an auto-negotiation mechanism that automatically selects the fastest possible link-up speed. An integrated LDO voltage controller supports the 1.2 V core through driving a low cost MOSFET.
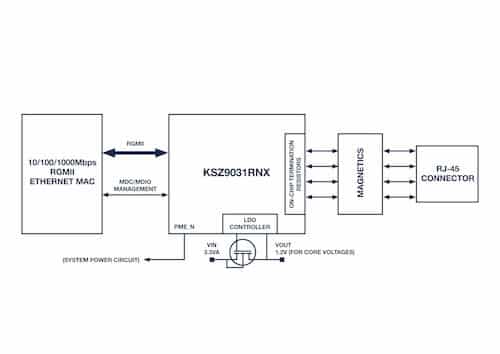
Another 1 Gbps device is Broadcom’s BCM89610 10BASE-T/100BASE-TX/1000BASE-T PHY (see Figure 4) that includes industry leading noise cancellation and jitter performance. As a result, this device is capable of being used with a broad range of cable qualities, offering potentially significant cost savings.
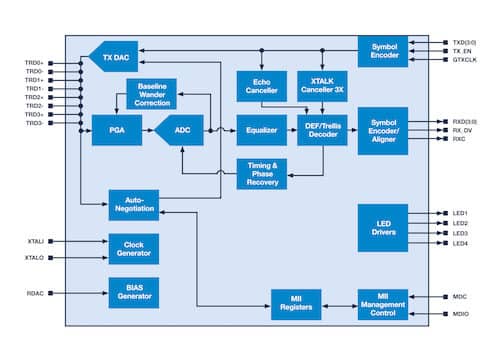
Summary
Vehicles are becoming an IT challenge with vast amounts of data being captured and created, all of which needs to be processed and transmitted around the vehicle. As more systems are added and existing functions expand, through higher resolution cameras for example, so greater bandwidth and data rates are required.
Older protocols are showing their age and newer protocols developed to be the next generation have not been widely adopted, leading the automotive industry to seek a new solution that is fast, low latency and low cost.
Ethernet is coming to the fore as it meets all of the technical requirements as new versions have been developed for automotive use. It also benefits from an existing ecosystem that includes software, tools and a wide array of low-cost, mass produced components. Possibly Ethernet’s most important attribute is its ability to be developed to meet the multi-Gigabit/second needs of the future.