Application of new materials, lightweight structures, vehicle safety and environmental regulations, hybrid vehicles, such energy systems as fuel cells, intelligent control systems, telematics, human-machine interactions, global manufacturing logistics and so on are changing the automotive industry into a complex interdisciplinary system.
The concept of green cars and other advanced technology vehicles are a means to reduce India’s dependence on imported fuel, uplift the economy and improve emissions. Green cars have been designed to objectively identify, organise and comprehend information and opinions on battery-run cars. Currently, various concepts specific to electric driving are being developed. India can only become a leader in electric mobility if battery vehicle systems can be produced domestically.
A battery electric vehicle (BEV) is powered by electricity stored in large batteries within the vehicle. The batteries are used to power the electric motor that drives the vehicle. The electric car’s navigation computer can show the driver, at the touch of a button, the driving radius within range under current battery charge, and the system can also calculate if current destination is within that range.
Most BEVs use regenerative braking, which allows the electric motor to act as a generator to re-capture energy that would normally be lost through heat dissipation and frictional losses. This, in turn, improves energy efficiency and reduces brake wear-and-tear.
BEVs benefit from high levels of torque found in electrical motors as well as smooth gear-less acceleration and deceleration. However, this is often more than sufficient for urban and city drivers. The reason for the short driving range is energy storage limitations of different types of batteries available in the market today. This can be overcome by using ultra-capacitors, which have very good charging efficiency and can store energy from braking to the next acceleration with high power in a short time.
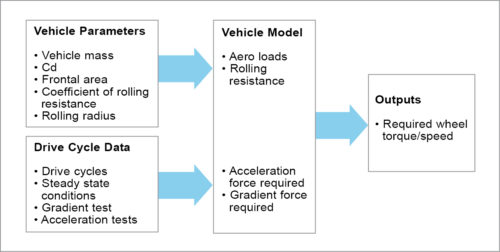
Ultra-capacitors have many advantages over traditional electrochemical batteries. These can completely absorb and release a charge at high rate, and in a virtually endless cycle with little degradation.
Application of new materials, lightweight structures, vehicle safety and environmental regulations, hybrid vehicles, such energy systems as fuel cells, intelligent control systems, telematics, human-machine interactions, global manufacturing logistics and so on are changing the automotive industry into a complex interdisciplinary system.
The vehicle motion control consists of two main blocks:
- Path controller, which as per desired path gives force and movement to the force distributor, which determines desired forces to be given to each motor
- Energy management controller, which calculates desired power needed from the power supply, determines state of charge and estimates overall traction force to be sent to the command integrator/controller unit
The command integrator and allocator block combines the requests coming from vehicle motion control and energy management units, and determines/distributes the torque request to each motor.
To handle EV stability while cornering or under slippery road conditions, the traction drive uses direct torque control and an adaptive-flux-and-speed-observer-based algorithm.
Among available induction motor control techniques, direct torque control appears to be quite convenient for EV applications. It has the advantage of not requiring speed or position encoders, and it uses voltage and current measurements only. Flux, torque and speed are estimated. Direct torque control also has a faster dynamic response due to absence of a proportional-integral current controller.
Input of the motor controller is the reference speed, which is directly applied by the pedal of the vehicle. However, typical advantages of direct torque control are not sufficient for low-speed operations and parameter variations. In that case, EV wheels are coupled to the induction motor via fixed gears. The induction motor is fed by the inverter and controlled by a direct torque control strategy.
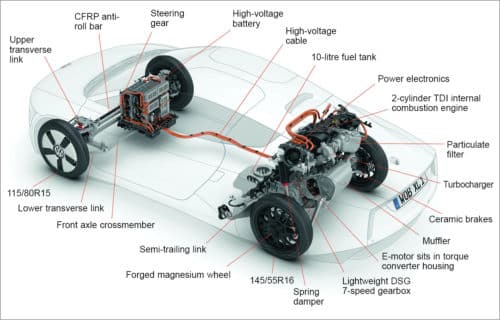
Speeds used by the speed controller are estimated using adaptive observers. Quantity provided by the steering wheel is added to vehicle reference speed for the external wheel and extracted from vehicle reference speed for the internal wheel. This generates induction motor reference speed.
Direct torque control references are obtained using proportional-integral controllers. Several advantages may be considered, including nearly sinusoidal stator flux and current waveforms, higher robustness regarding motor parameter variations, except stator winding resistance, higher torque dynamics, and easier flux and speed estimator implementation since coordinate transformation is not required.
V.P. Sampath is a senior member of IEEE and also a member of Institution of Engineers Ltd. Presently, he is patron of Semiconductor Federation of India.