Researchers at Worcester Polytechnic Institute (WPI), have pioneered a revolutionary method for producing lithium-ion battery electrodes, eliminating the requirement for solvents.
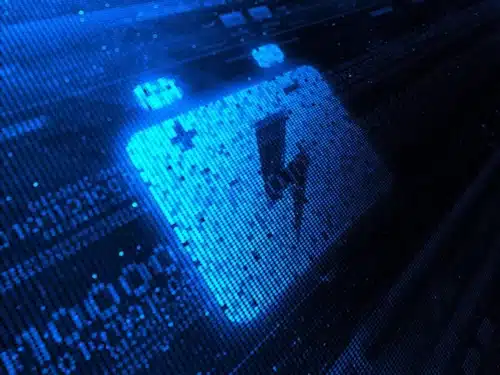
The present charging speed of lithium-ion batteries needs to be improved, and manufacturers commonly rely on flammable, toxic, and costly solvents, amplifying both production time and expenses. A common method to produce commercial lithium-ion battery electrodes involves blending active materials, conductive additives, polymers, and organic solvents to form a slurry. This slurry is then applied onto a metal substrate, dried using an oven, and divided into pieces for battery integration. The solvents are reclaimed through the process of distillation.
A research group led by Yan Wang from Worcester Polytechnic Institute (WPI), have spearheaded a groundbreaking approach to producing lithium-ion battery electrodes, eliminating the need for solvents. The innovative method offers greener, more economical, and faster charging electrodes compared to the current options, potentially bringing about a transformative revolution in battery manufacturing for electric vehicles.
The research team introduced a dry-print manufacturing technique that eliminates the need for harmful solvents and lengthy drying periods typically associated with traditional electrode production methods that involve slurries. Yan Wang, holding the position of WPI William B. Smith Dean’s Professor in the Department of Mechanical and Materials Engineering, , affirmed that this pioneering process is scalable and can reduce electrode production costs by up to 15%. Additionally, electrodes produced through this technique exhibit accelerated charging capabilities compared to those manufactured using conventional methods.
In contrast to conventional methods, the researchers combined electrically charged dry powders, allowing them to adhere when sprayed onto a metal substrate. The resulting dry-coated electrodes were subsequently heated and compressed using rollers. By eliminating the conventional drying and solvent-recovery steps, the researchers reported a remarkable 47 percent reduction in battery manufacturing energy consumption.
The researchers have collaborated with Texas A&M University and have co-founded AM Batteries Inc., a venture-backed company. AM Batteries Inc. is actively collaborating with Amperex Technology Limited (ATL) and other companies to accelerate the scaling up of solvent-free electrode manufacturing.
Reference : “Roll-to-roll solvent-free manufactured electrodes for fast-charging batteries” by Yangtao Liu, Xiangtao Gong, Chinmoy Podder, Fan Wang, Zeyuan Li, Jianzhao Liu, Jinzhao Fu, Xiaotu Ma, Panawan Vanaphuti, Rui Wang, Andrew Hitt, Yavuz Savsatli, Zhenzhen Yang, Mingyuan Ge, Wah-Keat Lee, Bryan Yonemoto, Ming Tang, Heng Pan and Yan Wang, 10 May 2023, Joule. DOI: 10.1016/j.joule.2023.04.006