Even as designers’ creativity comes alive with 3D-printed clothes and jewellery at a fashion show, elsewhere in the world a cancer-ridden bird stays alive with a 3D-printed bill, and a new-born child gets a new lease on life with a 3D-printed skull. Indeed, the emerging applications of 3D printing are awe-inspiring and packed with hope
Crescent, a 25-year-old Great Indian Hornbill, is one of the most loved birds in ZooTampa at Lowry Park, Florida (USA). When the zoo officials posted a picture of this winged beauty on their Instagram page last year with the tag line, “Crescent, our Great Indian Hornbill never misses a chance to strike a pose. Come out and visit her in our main aviary…,” little would they have thought that she would be inflicted by a potentially fatal form of skin cancer called squamous cell carcinoma.
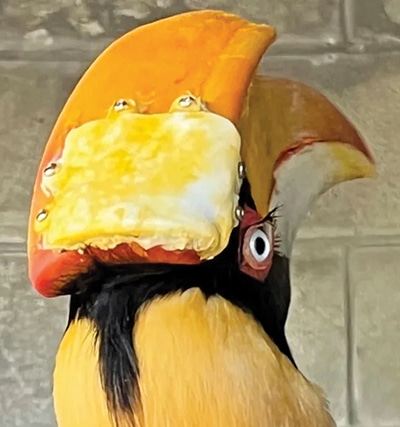
While the tumour is typically found near the front of the casque in hornbills, hers was in the back. This almost ruled out the possibility of a traditional extraction, as it would have exposed the bird’s sinuses. So, a team at the University of South Florida’s Radiology department printed a new casque using a Formlabs 3D printer and their new BioMed White Resin, a photocurable material that can be used to print biocompatible parts for prosthetic devices.
The material had just been developed by Formlabs, and they donated it to the team trying to help Crescent. The team not only printed a new casque but also a replica of Crescent’s head so that the team of veterinary surgeons could try the operation virtually before performing it on the bird—as it was a rare procedure, which had been done only once before by a veterinary surgeon in Singapore.
In January this year, the team removed the tumour and fitted the new casque on Crescent, who is now back in the aviary—as perky as ever. Luckily, it turned out that the resin was a perfect match for the yellow preening oils that keep a hornbill’s casque bright and shiny, so she also looks as pretty as ever!
As against the early days of 3D printing, or additive manufacturing, when objects could be created only with a few polymer based materials, we now have advanced processes that enable 3D printing with dozens of materials ranging from carbon fibre composites, metals and alloys to sand, tungsten filament, and bio-compatible materials. Understandably, the applications and possibilities have also expanded manifold.
Industry 4.0 is gearing up to use additive manufacturing capabilities to print tools and jigs, and end-use components too. The energy sector is using additive manufacturing to print parts for customised solutions, while carmakers are using it to customise luxury cars. The aerospace world is using it extensively to print lightweight but sturdy parts and components from special materials, while the food industry is using it to make customised confectioneries and personalised nutrition solutions.
3D Printing: A Quick Background |
3D printing, or additive manufacturing, is a technology that has been developing slowly and steadily since the 1980s. In simple terms, a 3D printer can take CAD file as input and print a three-dimensional object by depositing layer after layer of a suitable material. Hence, it is known as ‘additive’ manufacturing. In some rare cases that require extreme precision, a subtractive process might also take place, where excess material is shaved off the object. Over the years, several technologies have emerged, capable of printing with different materials, and with varying degrees of precision. Each generation, or each new process, aims to bring down the manufacturing time and costs, increase the precision, and widen the spectrum of materials that can be used. Now, materials ranging from gypsum and ceramic to wood and titanium are being used for 3D printing. As a result, the potential applications are also increasing. |
From construction to electronics, everyone seems to be exploring how they can utilise the potential of 3D printing. Let us share some of those insights.
Print a pill? Old news! Ready to print organs now
According to a report by Grand View Research, an India and the US based market research and consulting company, the global healthcare additive manufacturing market size was valued at US$1.6 billion in 2021. It is expected to expand at a compound annual growth rate (CAGR) of 22.6% from 2022 to 2030. The need for customised medical equipment like implants, the emergence of new 3D printing technologies that can economically print complex designs, and development of new biocompatible material capable of printing tissues, organs, dental fittings, orthopaedic and cranial implants are contributing to this growth.
Medical equipment like implants is very expensive to produce with traditional equipment, moulds, dies, and all the works. After all, most of these are comparable to works of art, tailor-made to fit a person. On top of that, these have to be produced quickly; sometimes it is a matter of life and death. The ability to swiftly develop prototypes using computer-aided design (CAD) makes 3D printing fast and economical.
Helping hand during the pandemic
3D printing rose to the occasion to support healthcare systems during the Covid-19 pandemic. Lockdowns crippled supply chains, but there was a growing need for supplies like personal protective equipment (PPE). 3D printing enthusiasts from around the world, university labs, and companies that had 3D printers started meeting this demand by printing goods like face shields and valves for respiratory machines. For example, 3T Additive Manufacturing Ltd and EOS produced more than 100,000 face shields for healthcare workers in the UK. Allevi Inc, a 3D bio-fabrication company, produced a model of the lungs of a person infected with SARS-CoV-2, which was studied by researchers at the Wistar Institute to understand the condition and find ways to treat and prevent it.
Prosthetics and exoskeletons
Earlier this year, 3D printing saved the life of a baby girl born with a critically-underdeveloped cranium—in simple terms, without a skull. A doctor approached Sygnis, a Polish deep tech company, just hours before the baby was due to be born. Armed with imaging data, Sygnis started 3D printing the skull using two different technologies, in case one failed. Within a day, they had the model ready—and the doctors completed fitting it within four days. The baby will require further treatment as she grows, and hopefully tech will find a way to help her survive.
Recently, Sygnis also produced another pre-operative model—the spine of a young child with meningo-spinal hernia and scoliosis.
3D printing is also proving to be very effective in the manufacture of exoskeletons for rehabilitation. 3D-printed exoskeletons are lighter, more durable, lower in cost, and a perfect fit for the person.
3D Printing Technology | Materials | Applications |
Sheet lamination methods, such as ultrasonic additive manufacturing and laminated object manufacturing | Paper, plastic, metal, any sheet material that can be rolled | Non-functional prototypes and models, multi-colour prints, casting moulds |
Directed metal deposition (DMD) or directed energy deposition (DED) | Metals like cobalt, chrome, titanium | Repairing high-end components, functional prototypes |
Material extrusion, most common being fused deposition modelling (FDM) | Plastics and polymers, including polylactic acid (PLA), polycarbonate, acrylonitrile butadiene styrene (ABS), nylon, polyetheretherketone (PEEK), thermoplastic polyurethane (TPU) and thermoplastic elastomer (TPE), carbon fibre filament | Electronic housings, form-fitting fixtures, investment casting patterns |
Material jetting, nano-particle jetting, drop-on-demand | Plastics, polymers, silicone, metals | Prototypes, medical models, design presentations |
Binder jetting | Polymers, metals, ceramics, glass | Metal parts, low-cost prototypes, sand casting moulds |
Vat photo-polymerisation, such as stereolithography (SLA), direct light processing (DLP), and continuous direct light processing (CDLP) | Plastics, polymers, resins | Injection moulds, prototypes and models, dental fixtures, medical parts |
Powder bed fusion technologies, including direct metal laser sintering (DMLS), electron beam melting (EBM), selective heat sintering (SHS), selective laser melting (SLM), and selective laser sintering (SLS) | Powder-based polymers and metals, including nylon, PEEK, non-toxic plant-based resin, stainless steel, titanium, aluminium, cobalt, chrome, copper, Alumide (a composite of aluminium and nylon), and Inconel (an alloy of chrome and nickel) | Functional metal parts, low-volume production, hollow designs |
There are also some open source projects, which aim to make low-cost 3D-printed prosthetics available to underserved populations across the world. Cyborg Beast, for example, is a low-cost 3D-printed prosthetic hand for children with upper-limb reductions. The designs are available under a Creative Commons license, so anyone can download, customise, and 3D-print them.
3D Printer in Space |
According to a recent news report, aerospace company Airbus is planning to send a metal 3D printer, Metal3D, to the International Space Station (ISS) in 2023, as part of its plans to establish an orbital satellite factory. According to Airbus, this will be the first metal 3D printer on the ISS. It will enable astronauts to print tools and parts like radiation shields. The company also says in the media report that future versions of the printer will be able to create objects out of lunar soil and recycle parts from decommissioned satellites onboard an orbital satellite factory. |
According to the Biomechanics Department of the University of Nebraska Omaha, the majority of the required materials are available at local hardware stores or online, costing approximately US$50. It takes around 2.5 hours to assemble the prosthetic hand, which weighs less than 200 grams. A similar device (made using traditional methods) would cost approximately US$4000 and weigh about 400 grams.
Blood vessels, tissues, and organs too
The emerging space of 3D bioprinting involves printing with cells and biomaterials, creating organ-like structures that let living cells multiply. These tissues and organ models help to understand diseased conditions better (for drug development) and for potential treatment.
Scientists at Technion-Israel Institute of Technology have created a hierarchical network of 3D-printed blood vessels capable of supplying the necessary amount of blood to an implanted tissue. For a tissue implant to be successful, it must first be permeated by the body’s blood vessels for it to receive the required oxygen and nutrients. To achieve this, the tissue is first implanted in a healthy limb of the patient’s body, and then shifted to the required location. This complicates and delays the process.
At Technion, the scientists have created a tissue flap in the lab, with all the vessels necessary for blood supply, so it can directly be implanted in the affected area. The new tech has been successfully tested on rats and will be tested on larger animals before it is ready for human use.
While previous experiments used collagen from animals in the bio-ink, here, Israeli company CollPlant Biotechnologies has genetically engineered tobacco plants with five human genes to produce collagen! According to the researchers, large blood vessels of the exact shape necessary can be printed and implanted together with the tissue that needs to be implanted. This tissue can be formed using the patient’s own cells, eliminating rejection risk.
A team of researchers led by associate professor Dr Akhilesh Gaharwar and assistant professor Dr Abhishek Jain, in the Department of Biomedical Engineering at Texas A&M University, have designed a 3D-bioprinted model of a blood vessel in healthy and diseased states. They have also developed a new nanoengineered bio-ink, which has the strength and optimal viscosity for smooth printing. The ink is printed into 3D cylindrical blood vessels, consisting of living co-cultures of endothelial cells and vascular smooth muscle cells, which maintain integrity of the arterial walls.
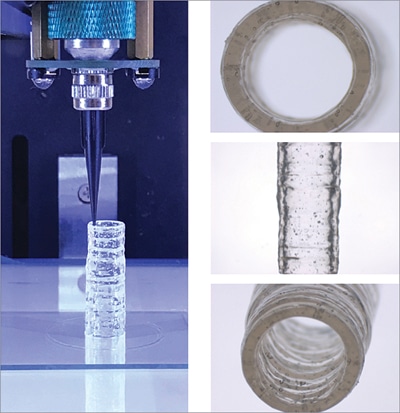
Please register to view this article or log in below.