This article describes how to get the framework on product requirements, basic design parameters, a conceptual clarity of various manufacturing processes required, and the quality assurance process by Quality Function Deployment (QFD). The final product design will, however, require further detailing. It will also require an analysis of cost, technology, and business viability
In my article titled ‘Developing Lovable Products to Beat Competition’ published in the January issue I discussed lovable products. A product needs to have certain qualities for being loved. But quality is a very elusive concept. We all understand quality as something that makes the object desirable.
Beyond this universally accepted concept, quality means different things to different people. Some customers may give more priority to the looks, some may prefer more reliability, some others may look for a lightweight product, whereas another group may want one that costs less. To cater to these different needs the product has to address multiple things to be successful in the market.
Sometimes, we may need different product models to address these needs. In this article, we shall focus on the process of systematically addressing these varied requirements of a product.
There are various approaches for systematic product requirement analysis. We shall discuss a rather simple and popular technique called quality function deployment, or QFD. This is a process of listing the requirements simply and concisely, comparing various benchmark products, and systematically evolving the product definition and its manufacturing process.
For QFD we start with listing the product requirements.
These requirements for a product come from various stakeholders. Part of it is from the people who will buy the product, then we have those who will use the product. Apart from these two groups we also need to address the requirements of those who sell, stock, and transport the product, the need of society at large, and the rules of the land.
If we fail to address all these varied needs, we shall end up with a bad quality product. So, our journey for product development has to start with discovering and documenting all these requirements.

The QFD process uses a set of four charts to systematically evolve the product definition, manufacturing, and quality assurance plans. The first chart is used to evolve product specifications to address the product needs. In this chart (Fig. 1) we list the product requirements in the first column.
Now, all requirements are not equally important. Some of the requirements may be just a wish, or what we call nice-to-have features. Other requirements may be strongly desired and may influence the buying decisions. The third category of requirements is the must-have features. Unless the product has those must-have features it is not usable.
We rate these priorities on a scale of 1 to 10, with 1 being for the least essential and 10 for the most important requirements. Typically, ratings 7 to 10 are reserved for requirements that are necessary for the product. Customers will not purchase the product if these requirements are not fulfilled. The next set of priorities is what sets one product apart from the other. These requirements get a rating between 4 and 7.
The rest of the requirements are what customers will appreciate but will not strongly motivate or influence them to purchase. Such requirements typically get a rating between 1 and 4. Understanding the priority of the requirements is as important as understanding the requirements.

Once we get a fair idea of the requirements and their priority, we should look at the existing products and benchmark and select the combinations of features for the product that we want to offer.
All these features and combinations can be quite confusing and difficult to handle. The QFD process provides a concise and systematic way to handle this huge amount of information. For QFD we create a chart to capture product requirement information. In the first two columns, we write down the requirements and their priority. The product needs to have a certain feature to address the requirements.
For example, if we say our charge controller should handle 600W of power at 24V, then the transistor or relay that will divert the power has to be rated for that current and voltage. One feature may address multiple requirements, or one requirement may get addressed by multiple features.
We write down these product features in columns, starting from the third column. We put the number 1 to indicate which of the requirement is addressed by which product feature. At end of the exercise, we should have mapped all the product requirements to product features. After the product feature columns, we write the benchmark products and rate them on performance against the product requirements.
This exercise gives us clarity on which product features address which requirements and the performance of other products against various requirements. In addition to the captured information, we calculate the relative importance of the product features by taking the weighted sum of the product of priority number and product feature mapping.
These numbers tell us which of the product features are very important and which are not so important. The importance ranking is required to save time and highlight the important features of the product.
The next task of the QFD process is to find the interactions between different product features. Some features are positively co-related whereas some other features may be negatively correlated. For instance, we may use drivers with higher power ratings to make our product robust and reliable, but that higher-rated item may be costly, which will diminish the attraction of our product. Clarity on how different product features are related is an important step before we decide on the target specifications of our product.
To decide on the target specifications, we need to use the feature importance number. Important features should be decided after careful study and prototyping. Target on less important features may be decided based on a comparative feature study of the competition.
We start with various requirements of the product, such as:
Performance: Power rating, service life, reliability, installation, and maintenance
Physical: Size, weight, environment
Regulatory: Environmental hazards, safety norms, disposal
Logistic: Packaging, protection, physical dimensions
Economic: Price, profit margin, sales volume
Apart from these basic requirements we also need to provide features that make the product attractive. In our previous article, we explained how we can increase the attraction of our charge converter by making it smart. We need to consider those interactive features as well.
At the end of careful consideration of various product features, we finally get a list of the required product features. QFD process captures the information and the final outcome in a single chart and clearly shows how the product requirements are addressed by product features. While requirements are a little vague, product features give us specific figures that form the basis of product design. The filled QFD chart for the charge converter (Fig. 3) shows this process.
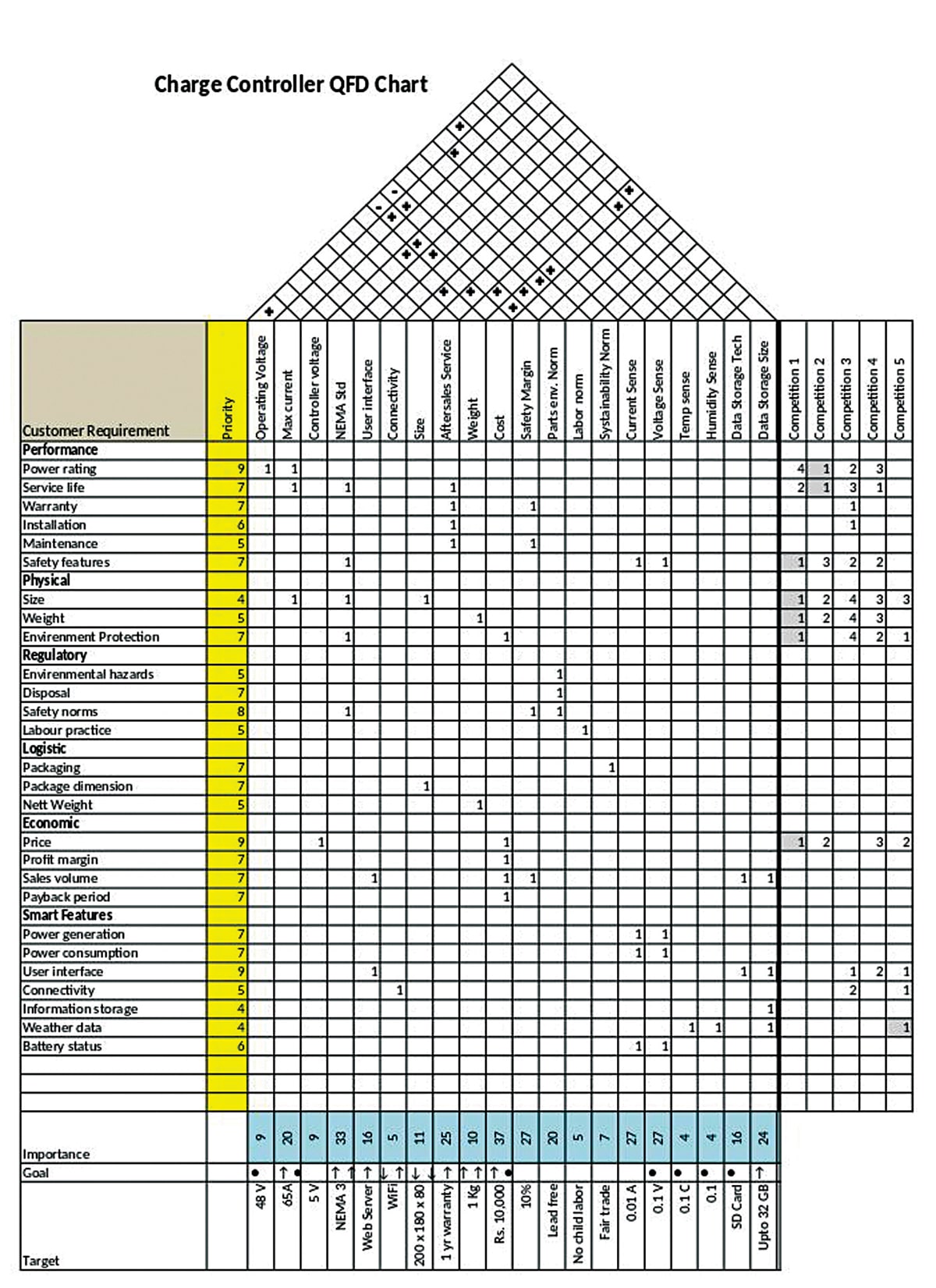
For the sake of commercial confidentially I have changed the competitors’ product names and instead called them Prod. A, Prod. B, etc. The highlighted cell indicates where we want our product to be in terms of the requirements. The triangular portion shows the correlations between different product parameters. Just below the parameters, we write the target values for the product.
We shall take a specific example to show how the product specification is determined. In the requirement, we noted that the charge converter should be able to handle the power requirement for a small family. Looking at the other benchmark products we find the rated power varies from 500W to 1,200W.
We want our product to be of premium quality and so decided that it should be able to handle 1,500W power from the alternator. It is also decided that the operating voltage of the converter will be 48V. This gives the current rating as 1500W/48V= 31.25 amps. We add a 10% safety margin and set the product specification as 35 amps and 48 volts.
The QFD process uses four such charts to describe the complete product development plan (Fig. 2). In the QFD jargon, we call these charts a house.
The first house is used to arrive at the product specifications from the product requirements. While product requirements are generic and qualitative, product specifications are more quantitative values. In the second house, we translate the product specifications into product design parameters. The third house gives us the manufacturing plan and the fourth house gives us the quality assurance plan. These four charts together describe the high-level product development plan.
Fig. 3 shows the QFD chart for the first house. Here we derive product specifications from the list of requirements. Requirements are the list of things that we want our product to perform. We list different requirements in the first column of the QFD and then take an evaluation on the priority of these requirements.
Ratings 7 to 9 are reserved for requirements that are in the “must have” category. Rating 1 to 3 is a “nice to have” kind of requirement. These ratings indicate that customers would not care much about the requirement. The rest of the requirements are rated between 4 and 6.
Next, try to figure out the product features which will address the requirements. These features we put in the columns starting from the third one. We also put a mark ‘1’ to indicate which product features address which requirements. There can be more than one feature to address a particular requirement. Also, one feature may address multiple requirements.
Next, we compare our target product with the ones that are available in the market.
Competitions 1 to 4 are existing charge controllers. We took a weather station to compare the features of connectivity and user interface (Competition 5). We rank the product against the requirements. Shaded cells indicate the features that we selected for our product.
But, before selecting the target feature, we must complete the top portion, the roof. The triangular section shows how different product parameters are related. For instance, higher operating voltage has a negative effect on cost and safety margin. Higher current on the other hand will push up cost and safety margin.
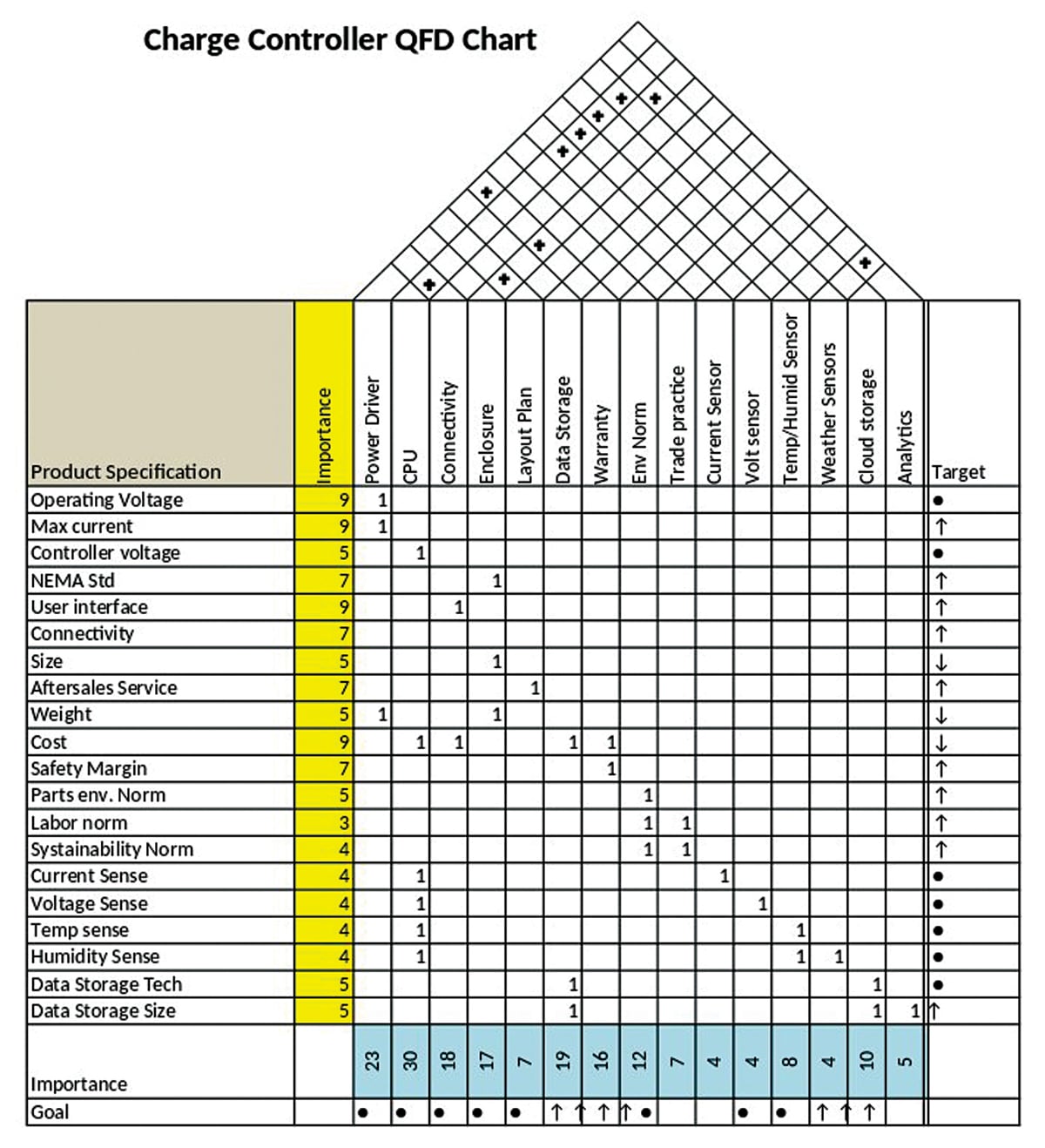
Once we get a clear picture of the various interactions then we can select which required feature from the customer will be most suitable for our target product. As you see here, it is not necessary to take all the features from a single product. Some of the features we may decide to use can be our own.
Next, we compute the importance index of the parameters. These parameters address multiple important requirements. For instance, in our case, cost, followed by NEMA Standard, are the most important parameters. Based on the competition benchmarking we then decide our target values for each of the parameters.
Finally, we decide that our charge controller will be for a 48V alternator with a max current rating of 65A. It will have NEMA 3-level environment protection and be housed in a 200mm×180mm×80mm box. It should weigh around 1kg and cost around ₹10,000. It will save data on an SD card and have a Wi-Fi connection to send operation data to a cloud server.
We must mention here that at this juncture the values that we select are just indicative figures that we picked up from the comparison of similar products from the market. Subsequent steps of design help us to validate, modify, and get further details of the product design.
In our next step, we use the product specification information to get the first-level design specifications. Product specifications are things that are visible to the customer. Design specifications are details that tell us how to make the product. Design specifications are the internal details that are not visible to the customer.
For getting the design specifications, we start with the list of product specifications. This is the set of features that needs to be delivered by our product. Next, we give an importance rating of the product specifications. Some practitioners recommend using the same important figures that we got in the first chart.
Product design is primarily an engineering design exercise. One should not blindly follow the figures that have come from intuitions and group opinions. In my experience, re-evaluation and moderation of the important figures in the second stage give better focus on the design process.
In the second house, we list the high-level design parameters in the columns and then map these parameters to product specifications. In the end, we examine the co-relations between design parameters and decide on the design parameters.
Design specifications and the decided specifications we list in the third house, the manufacturing plan. Design and manufacturing plan must emerge together. One needs to look at various alternatives, work out production volume, and then decide on the most profitable manufacturing route. The cost of the part as well as the production costs have to be worked out before we take the design decision.
The charge controller needs to handle rather a large current. The frequency of switching on/off is less. All the competitions use a relay for this operation. We also decide on a relay for the main current driver operation. In our device, we need to sense two analogue voltages and get data from the humidity and temperature sensor using an i2C connection.
As the expected production volume of our product is small to medium, we select a readily available microcontroller module, namely, Arduino Pro-Mini. For internet connectivity, we select a companion Wi-Fi chip, ESP8266. Likewise, we decide on enclosures, sensors, environment norms, and software options. These details are put in the third QFD chart (Fig. 5).
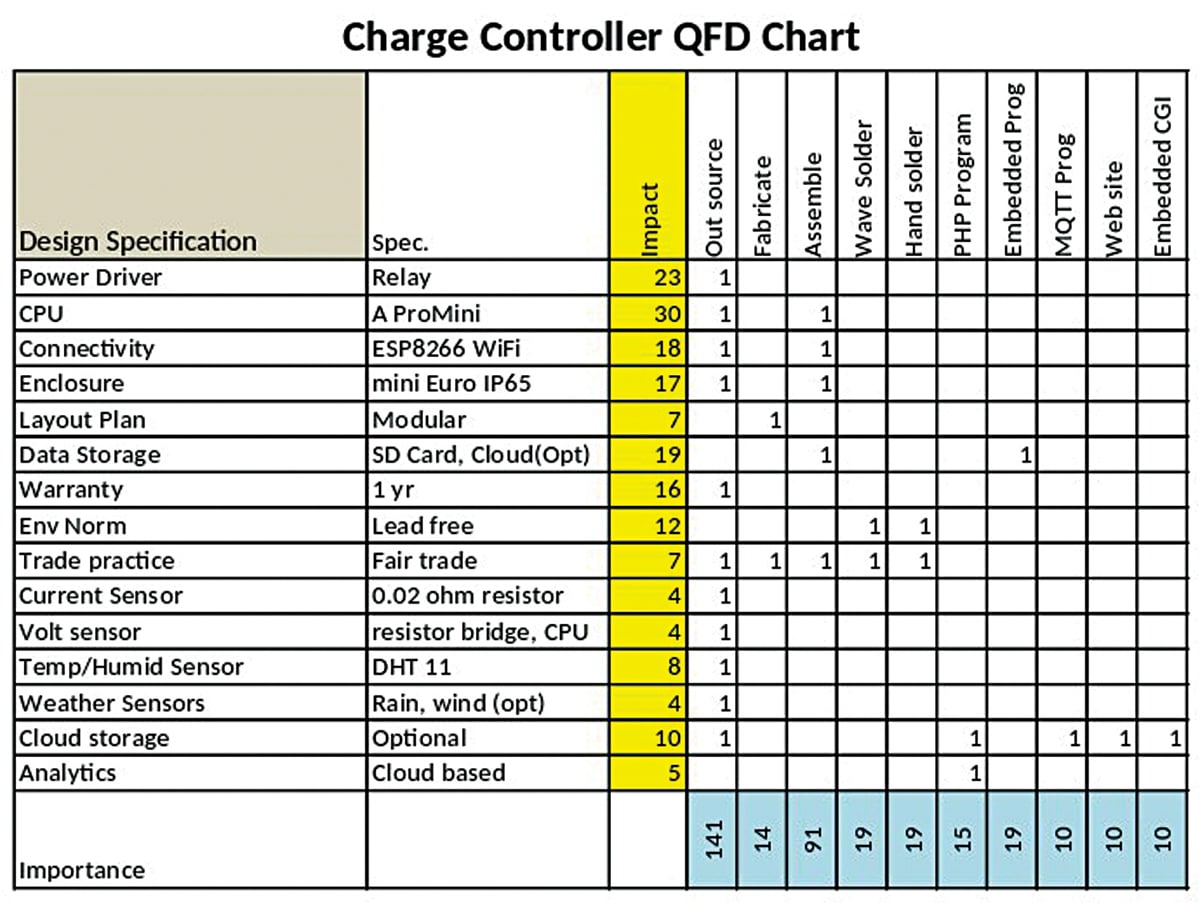
The third chart helps us prepare the manufacturing plan for our design. Here we put the manufacturing process in the columns and figure out the manufacturing processes for various parts. In the impact column, we use the figures from the second QFD chart. Summation of the impact factors gives us the importance of manufacturing processes. Manufacturing processes that have a high impact on the product need close monitoring to ensure quality.
In the fourth house, we decide on the quality assurance plan for our product. Here we decide how to monitor the process and ensure the quality of the output. As you see in Fig. 6, we may adopt a similar quality control strategy for multiple production processes.
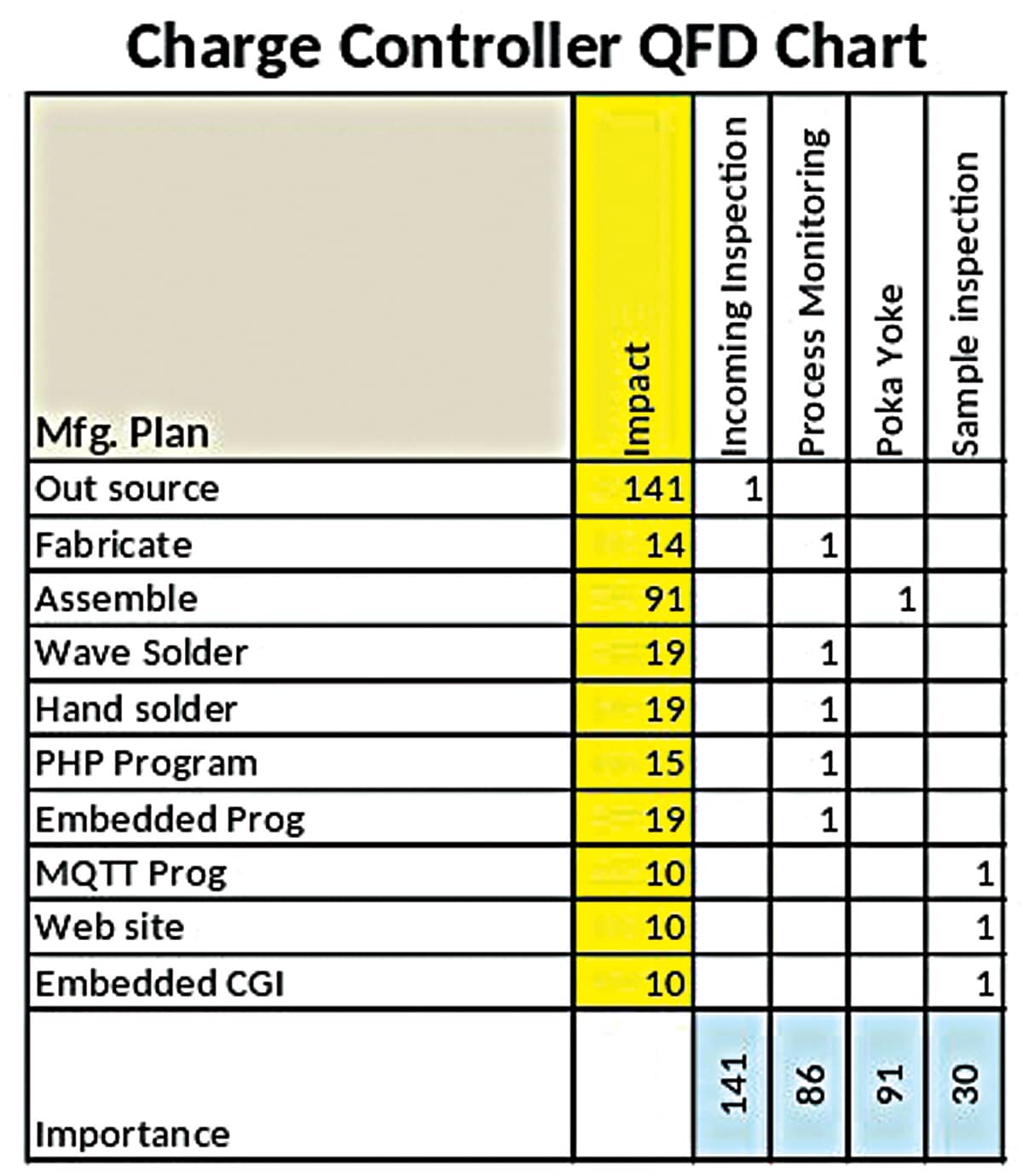
Like our previous step, the importance value of stage 3 becomes the impact of stage 4. The summation of relevant impact factors gives importance to the quality control process. A quality process with high importance value, like the incoming inspection in our case, needs to be given more focus. We need to develop elaborate plans to ensure proper control.
These four QFD charts give us conceptual clarity of our product design. QFD process ensures that all stages of product design, manufacturing, and quality assurance stay aligned with the customer’s requirements.
What we got after this exercise is the base-level product concept. It is a framework on product requirements, basic design parameters, a conceptual clarity of various manufacturing processes required, and the quality assurance process. It is not the final product design.
The final product design will involve further detailing. It will also require an analysis of cost, technology, and business viability. Finally, product and business validation has to happen. In our next articles, we shall explain these processes that are needed for successful product design.
Soumyanath Chatterjee is a former TVS Motors Chair Professor at the Industrial and Systems Engineering Department, IIT Kharagpur. His expertise is in Product Development and Supply Chain Management