Computer and physical processes are meant to be seamlessly integrated in a cyber-physical system (CPS). Thus, computers and networks can keep track of the actual manufacturing process at a given facility. Industry 4.0 is built around the concept of “smart factories,” which are facilities that are equipped with advanced technology. As the name suggests, a Calm-system is used in smart factories. A tranquil system is one that is capable of coping with both the real and the virtual worlds. To put it another way, they’re known as “background systems.” Objects in the immediate environment are recognised by a calm system. The Internet of Things and the Internet of People must allow objects, machines, and people to connect with one another in real time. This is the single most important principle that determines whether or not a factory can be considered intelligent.
CPSs need to be able to construct and recreate a digital version of the real world they’re working in. CPSs must also be able to keep an eye out for items in the immediate vicinity. Everything must be replicated in some form or another.
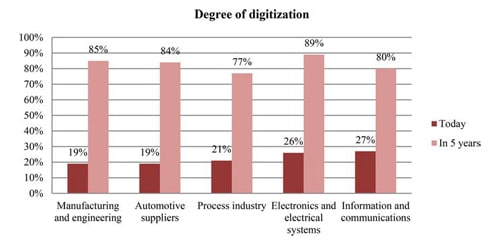
The autonomy with which CPSs can carry out their duties. As a result, things can be made to order, and problems can be solved creatively. As a result, production can be more adaptable. The topic is delegated to a higher level in the event of failure or competing goals. It is still necessary to have quality control measures in place, even if new technologies are being used.
Real-time data collection and analysis are critical to the smart factory’s ability to make informed decisions. Internal processes, such as the breakdown of a machine in a production line, are also examples of this. Intelligent objects must be able to recognize a problem and delegate work to other operating machines in order to remedy it. In addition, this contributes substantially to a company’s ability to adapt and optimize output.
Customers must be at the forefront of the manufacturing process. Connecting people & smart appliances via the Internet of Services is essential to creating products that meet the needs of customers. The Internet of Services plays a critical role in this scenario.
A Smart Factory’s flexibility in responding to changing market conditions is critical in today’s fast-paced economy. An average corporation would probably need a week to analyse the market and make changes to its output as a result. Seasonal variations and market trends necessitate that smart factories be able to respond quickly and smoothly to these shifts.
ML and Industry 4.0
It is via advancement of machine learning that Industry 4.0 is beginning to take root in enterprises as well as on manufacturing floor. Computer systems and algorithms can learn and improve on their own using machine learning, which is a type of artificial intelligence. Manufacturing has seen enormous improvements in optimization thanks to machine learning. Manufacturers can develop a “smart factory” by improving manufacturing systems to work with machine learning. Automation and data collection are key components of smart factories, which are digitalized versions of traditional manufacturing. Companies can make better judgments because to advanced analytics provided by this data collecting. The ability of machine learning to boost efficiency without materially altering existing resources is likely to be one of its most noticeable benefits in the manufacturing industry. Real-time error detection is an example. Smart factories can rapidly analyse the quality of their products by utilizing smart devices on the production floor. ML-enabled video streaming devices can track the progress of a product from conception to completion. Afterwards, the system will be able to quickly review each frame and look for any possible flaws. Engineers may get real-time actionable insights to fix flaws using ML, video analysis, & live performance monitoring.
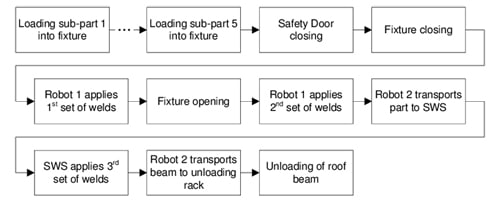
If you’re in the manufacturing sector, you’ll be able to inspect more quickly than ever before. A faster manufacturing line, as a result of the shorter inspection times, translates into greater sales. In addition to giving manufacturers better data and details, the capacity to interact problems in real time allows manufacturers to significantly cut down on both downtime and scrap that happens when there are only a few people watching. Predictive insights provided by machine learning systems allow industries to move from reactive environments to those that prevent problems from occurring. Predictive maintenance refers to the ability of machine learning to detect manufacturing process faults before they occur. Preventative maintenance are significantly less expensive than dealing with a damaged machine or a process which has already cost the company a lot of money in waste. Additionally, it minimizes the financial toll of a significant breakdown. Theoretically, smart factories have a lot of promise; nevertheless, there is enough of evidence to suggest that they can actually have a significant impact on business. Using a smart factory as an example, Harley-Davidson cut their manufacturing cycle from 21 days to just 6 hours. A $ 300 million reduction in production costs has been achieved as a result of this adjustment. Many other companies can learn from the achievements of Harley-Davidson. GE, Audi, and Siemens, to name a few, have all cited comparable success stories. To be clear, this does not mean that smart factories are only beneficial to large corporations.
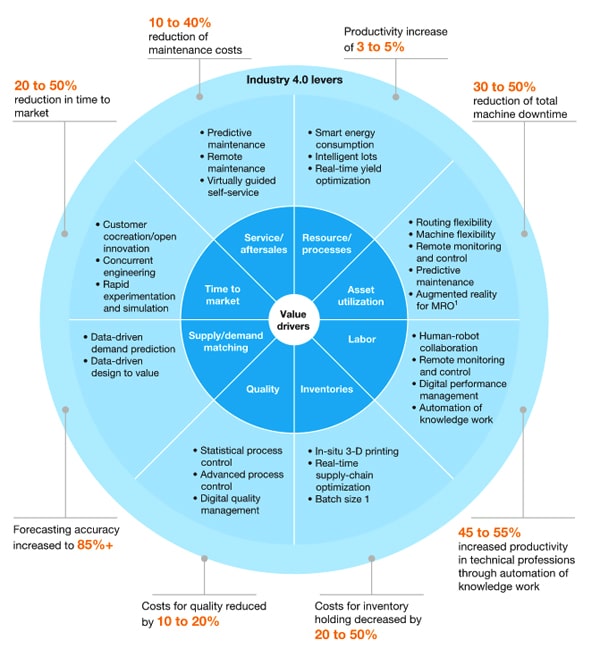
Applicability of Industry 4.0 in the current ERA
The worldwide COVID-19 pandemic has an impact on companies. Manufacturing is the same as any other business. If you use digitalization as well as machine learning in the workplace, though, this problem can be solved. Companies can now keep an eye on different plants from afar thanks to tools like corporate monitoring platforms. This means that workers don’t have to spend their time manually collecting data. . This is a good thing. There has been a rise in social distancing, which makes it safer and easier for both employees and businesses to keep track of factory health without having to be on the floor with them. People are afraid of new technology and prefer to use things that have worked before. This has kept a few older factories and businesses from adopting a Industry 4.0 model because they don’t like change. Industry 4.0 is becoming more evident in a world where more and more people work from home, even though 2020 has some unique problems. If you’re in an industry that hasn’t changed a lot, it’s safe to say that Industry 4.0 tools like tele monitoring systems and machine learning will help you stay in business when the storm comes. Machine learning’s impact on manufacturing can’t be overstated, as evidenced by the wide adoption of Industry 4.0 and the many success stories of smart factories that already hit the market. This shows that machine learning has a big impact on manufacturing. These aren’t just small consequences, either. Immediate efficiency and cost savings can be achieved by using Industry 4.0 techniques. These techniques also make it possible to make savings that are hundreds of millions. Producers should be on the lookout for big growth as Industry 4.0 progresses and is used more and more. In order to make Industry 4.0 and the smart manufacturing possible, there are three things: cyber-physical systems, the Internet of Things, and the Internet of Systems. Machines that can learn and develop as more data is available to them will help us make our factories more productive and efficient, and we will cut down on waste. When machines are connected to each other digitally, they work together to make and share information. This is the real power of Industry 4.0, though.
Improve logistics and supply chains: New information can be accommodated by a connected supply chain. Connected systems can anticipate delays in shipments due to weather and alter production priorities accordingly.
It is becoming increasingly common for shipping yards to use autonomous cranes and trucks to speed up the process of receiving shipping containers from the ships.
This once-exclusive technology is now available to businesses of all sizes, making robotics more accessible than ever before. There are numerous ways in which autonomous robots might help producers, from picking products at a warehouse to preparing them for shipment. The employment of robots in Amazon’s warehouses reduces expenses and allows for more efficient use of floor space.
Since its invention a decade ago, additive manufacturing (3D printing) has advanced enormously and is now widely employed for mass production. Many new avenues for production have been opened up because to metal additive manufacturing.
The Internet of Things (IoT) is a network of interconnected electronic gadgets that is a fundamental component of Industry 4.0. Using the cloud to store data allows businesses of all sizes to benefit from each other’s expertise, as well as give smaller businesses access to technology they wouldn’t otherwise be able to afford on their own.
Despite the fact that the full picture of Industry 4.0 may not be clear for another 30 years, companies that have already embraced the new technologies are now reaping the benefits of Industry 4.0. At the same time, these businesses are pondering how to improve the abilities of their current employees so that they can take on the new tasks enabled by Internet 4.0 and how to find qualified candidates for open positions.
There are chatbots, which are computer systems that allow users to communicate with them via text or speech. They can be used to receive information or conduct tasks, eliminating the barriers to obtaining technological solutions. Their primary function is to assist customers during the purchasing process or act as filters for consultations with human experts who specialized in specific fields. With their 24/7 support and cost-savings, they can help you learn from the most prevalent issues.
Conclusion
IoT and Industry 4.0 are trends that will have a profound impact on business in the next few years. In addition to large corporations, small and medium-sized businesses will be affected by the transformation. Data collection and analysis is becoming more accessible because of the lower cost of the hardware required. We’ve seen six different uses for this technology so far, but it’s just a taste of what’s possible. The concept of “Industry 4.0” represents a sea change in production methods. Manufacturing will be pushed to a new level of efficiency and productivity by the new concept. Not just that, but clients will also appreciate the new level of individually customized products that may have never ever been available before. As previously stated, the financial rewards are enormous. To ensure a smooth transition, there are still a number of issues that must be addressed. Large corporations and governments alike need to pay attention to this. It’s critical to keep pushing the boundaries of research and experimenting in these areas. The overall picture is good, notwithstanding doubts about privacy, security, and jobs. The industrial industry will never be the same again if such an approach is taken.