A well-orchestrated interplay of digital twins, the Internet of Things, and artificial intelligence—with scalable apps, communication networks, and immersive virtual reality—the emerging industrial metaverse spells savings and sustainability for industries, across manufacturing, construction, grid, infrastructure, transport, and more.
Honestly, the moment someone says metaverse, we think of a hi-fi gaming environment, which people enter as avatars to play games or for social networking. We also know that companies, ranging from carmakers to banks, have started using this as a platform to engage with customers and showcase their products and services. It is a great place for brand promotion with celebrities and companies selling collectible non-fungible tokens (NFTs), virtual merchandise, and other fancy stuff. Unless you take a deeper look, it looks like just another marketing channel.
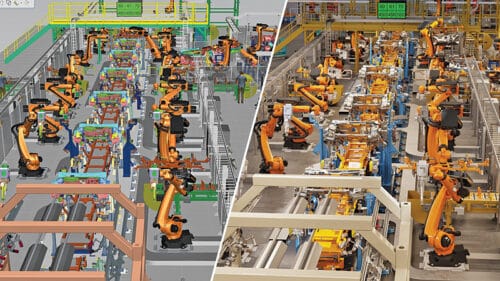
Silently, behind all this hullabaloo, industries have started using the metaverse and associated technologies for real tangible gains. This emerging application of the metaverse—generally referred to as the industrial metaverse—is likely to grow even faster than commercial and consumer spaces as the benefits are near-term and measurable. “The metaverse is quickly getting sub-segmented into various streams, influenced by the business domains. A metaverse for gaming has different applications and needs as compared to a metaverse that becomes a shared space for retail experiences. Similarly, industrial metaverse is evolving into a virtual realm where the digital world of factories integrates into a seamless network of supply-chain operations to create a high-touch product and service experience,” explains Umang Garg, Managing Director, Global Practice Leader, Nagarro.
The metaverse, which according to a recent McKinsey report has the potential to generate up to $5 trillion in value by 2030, is going to be a big force in the digital transformation of industries.
Decrypting the industrial metaverse
Emerging technologies are dynamic in nature—and it is difficult to nail them down with a globally-accepted definition. So, let us try to understand the industrial metaverse by means of its evolution rather than its definition.
Let us start with the digital twin—a technology that, according to a GE blog, has been around since 2002. It started as a product lifecycle management (PLM) tool for complex systems such as spacecrafts. In the early years, it was just a digital model of a physical system, somewhat like a prototype or blueprint, using which you could run tests and validate a design upfront before building it. Over time, the digital models were paired with specific instances or physical objects by adding data such as its dimensions, location, working conditions, etc.
Enter the Internet of Things (IoT). Sensors and actuators were added to the physical object and the data collected by these was fed to the digital twin in real time, making the digital twin a virtual mirroring of the current status of the physical object. With it, you could actually get real-time information about how a physical system is working, and even control it through the actuators. As a next step, environmental data was also fed to the digital twin, which helped understand how the system reacted to changes in the environment.
Fast-forward to the present. By adding intelligence to the digital twins, by way of analytics, machine learning (ML) and other algorithmic models, it has become possible to predict and prevent errors, and tune the system for maximum efficiency. With plug-and-play sensors and actuators, high-speed communications, industry-specific cloud based analytics, and intelligence tools, it is quite easy and cost-effective to implement a digital twin today.
How can the metaverse help industries? |
|
However, the real story begins only now. These standalone digital twins must be networked to gain real, strategic advantage! Networks of digital twins help an organisation understand the interplay of various systems—how one affects the other, patterns, trends, and so on.
Now, put this network of digital twins on a private metaverse and let your employees access it through their avatars. They can, virtually, be in the scene, watch a machine work, and even feel it heating up due to environmental factors. Derick Jose, Co-founder of Flutura Decision Sciences and Analytics, explains in an interview to YourStory: “For example, we are working with energy companies that have a complex array of equipment whose health we are predicting in real time. A reliability engineer can enter the industrial metaverse, look at the subsystems of the process in the metaverse environment, and decide what is the next best action to undertake.”
This ability leads to numerous applications and benefits, such as training new users without risk, identifying and preventing errors before they happen, understanding the impact of design or process changes before implementing them, and more.
Next, bring some of your key stakeholders like vendors, collaborators, and customers also into the metaverse. What you get is a complete virtual enterprise spanning the entire value-chain. You no longer need to visualise but can see what happens down the line. Say, when supply of cotton goes down in the rainy season, or when demand spikes during Diwali, you can tweak the system to meet these contingencies and test the solution in the virtual world, before making the change for real.
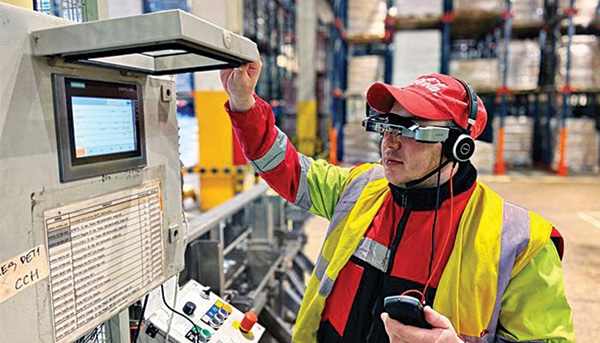
Metaverse in Industry 4.0
“We think of Industry 4.0 as an endeavour to build a connected enterprise that creates an ecosystem of a smart factory, connected workers, connected customers, connected products, and smart services. In such a connected enterprise ecosystem, there is a natural convergence between the physical and digital world. The metaverse is expected to play an important role in enabling this ‘phydigital’ convergence. The nature of the metaverse experience for industrial enterprises would vary based on the nature of the company and its products and services. Some common trends and themes that we expect to transform into popular use cases are employee engagement, employee training, product demonstration centres, virtual events, product digital twins, product design collaboration, and multi-party interactions,” says Garg.
Immersive human-machine interaction, exemplified via a digital twin is a good reflection of such a paradigm. These digital twins can be of different types: process, product, or system. Each of these types of digital twins can be at varying levels of complexity—from a simple replica of a physical world item to a dynamic bi-directional exchange of data between a physical machine and its digital twin.
“The fourth industrial revolution provides the opportunity to connect the physical and digital worlds aiming to accelerate change in technology, aligning to the increase in interconnectivity and automation across the business ecosystem. The digital twin provides a virtual representation to an actual or physical asset (product and/or system). The advancements in the industrial metaverse take this further, allowing a new representation of products and systems in a new channel of delivery expanding the market and market awareness to a new level. This may also provide prospects with the ability to virtually see and use the product or offering prior to purchasing,” says Paul Nashawaty, Senior Lead Analyst, Application and Infrastructure Modernization, Enterprise Strategy Group, a division of TechTarget.
Who should go for it and why?
Actually, everyone—organisations small and large—can think of implementing the industrial metaverse. It is not doable overnight; the industrial metaverse is a long-term pursuit, but it is worth it because the benefits are also longstanding. Thankfully, this is not a tech implementation that you have to finish in one shot—the train can come later, but you can start laying the track today.
Hendrik Witt, Chief Product Officer, TeamViewer, says, “Industrial metaverse technology can be harnessed and applied to any industry and across the entire industrial value chain to enable hands-free work with digital information in order to gain speed, improve efficiency and productivity as well as lower costs and error rates. Be it in onboarding and training, logistics, assembly, maintenance, or after-sales service.”
“Some of the initial benefits we see of adopting the industrial metaverse are in design and engineering, testing and validation, and training. In design and engineering, the industrial metaverse can enable the entire organisation to get immediate insight in the impact of design changes by distributed teams on all different disciplines. For testing and validation, the combination of photo-realistic environments with multi-physics simulations enables to test all kinds of scenarios and training autonomous systems through machine learning and synthetic data. And when it comes to training and closing the skills gap, the industrial metaverse will enable virtual training for all kinds of scenarios or hazardous situations and enable remote access to expert skills, empowering non-expert employees to solve problems,” says Dale Tutt, Vice President of Industry Strategy, Siemens Digital Industries Software.
“Some early adopters in the industry are exploring its potential to uncover new interaction and business models. For instance, a multinational oil and gas company is training its employees for safety in deep water oil production with virtual reality (VR). The company is using VR to transfer knowledge from one team to another and saving enormously on time. A leading defence equipment manufacturer is using smart glasses for 30% faster outcomes and 93% enhanced accuracy. In pharmaceutical warehouses, professionals are now assisted by head-mounted gear that mitigates safety risks, allows remote support, and aids in quality assurance by facilitating remote audits and process improvement. Automobile heavyweights are using metaverse precursor technologies to create and test designs collaboratively,” says Immanuel J. Kingsley, Metaverse Technology Officer, and Head of Innovation Lab at Hexaware Technologies.
Sadaf Siddiqui, General Manager – Industry Marketing, Keysight Technologies says, “We are talking about a massive industrial revolution which will be enabled by 5G. Some of the exciting pointers are predictive maintenance—to reduce downtime, and efficient analytics—to optimise resources and improve performance. The metaverse aspect will bring in remote connectivity option as well, wherein multinational setups can then be called as ideal global setups.”
Garg asserts that the industrial metaverse is relevant to every sub-segment of industrial companies across a range of use cases. “For example, manufacturers of complex and large industrial machines can demonstrate their product in a virtual factory environment within the metaverse, without having to worry about transporting this equipment to different demonstration locations. To enhance productivity and safety, mining companies or equipment manufacturers for the mining industry can create a digital twin of their operations or of their products. Similarly, manufacturers of industrial products, whether fasteners or chemicals, can virtually train workers who handle their products in correct application and usage while creating what-if simulations to teach the handling of special scenarios,” he says.
Tech components of the metaverse
“Digital twin is strategic as it helps to understand how the physical counterpart will behave under diverse set of operating conditions. Some of the other key components can be AI, VR, software intelligence, data analytics. There is no pre-defined standard model—it depends on what level of intelligence or automation we want to introduce into the segment. This can also be scaled up or down depending on the requirements and needs,” says Siddiqui, adding that the crux remains around smart connectivity with a high level of software intelligence.
Garg explains that, “The metaverse is a virtual collective shared space that is persistent, interactive, and immersive. It can be public or private, depending on the access privileges of its users. Technologies such as extended reality, blockchain, the IoT, and AI form the core of a metaverse ecosystem.” Extended reality (XR) is an umbrella term that covers virtual reality (VR), augmented reality (AR), and mixed reality (MR).
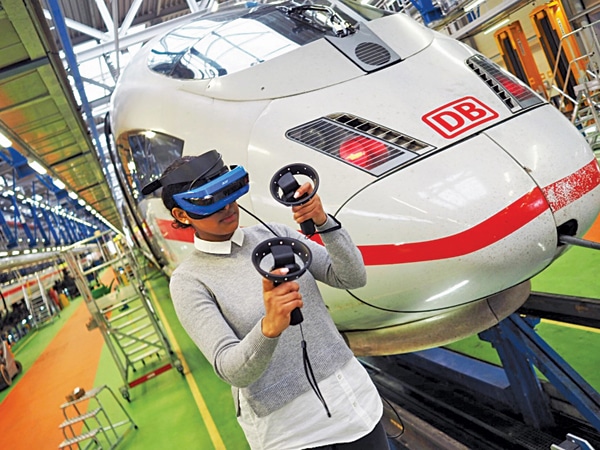
Digital twins
Very simply put, a digital twin is a virtual representation of a physical entity—product or process. Sensors capture operational and environmental data and stream them to the digital twin on the cloud. This is augmented with enterprise systems data—manufacturing execution systems (MES), enterprise resource planning (ERP), computer-aided design (CAD) models, etc. The physical and virtual realms meet using edge computing technologies.
Artificial intelligence (AI) discovers insights from the data—the more data there is, the better the AI system becomes. Feedback goes back to the physical world through actuators and decoders. This is the operation of a simple digital twin. In the industrial metaverse, multiple digital twins will be integrated.
By using digital twin technology right from the design phase, it is possible to test and validate designs of products and processes to mitigate errors. Boeing is building its next major plane using digital twin tech. In a press release, the company explained that 70% errors arise in the design stage. So, if more and more errors and discovered—and rectified—in the digital twin, then there will be less possibility of errors in the final product.
Current technologies, like that made possible by the Siemens Nvidia collaboration, enable photo-realistic, physics based representations of the real world. For example, if you simulate a difference in temperature or a part failure, the digital twin will react exactly like the physical asset would.
McKinsey predicts that digital twins will be a $48 billion business by 2026. A Grand View Research report suggests that the digital twin market may reach $86.09 billion by 2028, fuelled by Industry 4.0 use cases.
The Internet of Things
The industrial metaverse is nothing without the IoT—a fast, interconnected system of edge devices that collects and distributes data via the cloud. According to a report by IoT Analytics, the global number of connected IoT devices was 14.4 billion as of May 2022, and likely to go up to more than 27 billion connections by 2025. A lot of research is happening on reducing the size, power consumption and electromagnetic interference in IoT devices.
Communication systems
Communication needs to be fast (to keep it really real-time!), secure, and reliable. High bandwidth networks are needed to ensure proper delivery of AR content, without distortion. 5G promises the high bandwidth, low latency network that the industrial metaverse needs. Ericsson is building city-scale digital twins on the Nvidia Omniverse to help accurately simulate the interplay between 5G cells and the environment for maximum performance and coverage. That’s what one calls a symbiotic relationship!
According to a recent report by electronics-manufacturer, Molex, enterprises are moving to digital or software-defined circuits mainly to minimise intrusions that corrupt signals in analogue circuits. Digital circuits are not immune to noise, but they are known to be far less problematic. “To help our customers deliver stable and high-quality immersive experiences, we take extra steps in our products,” says Stephen Drinan, Director of Wireless Connectivity at Molex. “For example, with our 60GHz RF chips, we incorporate re-timers into the chip, eliminating signal integrity concerns with high-definition video.”
Data analytics and artificial intelligence
You collect data, fine, but what would you do with it? Once the data is aggregated, digital twins would use AI and ML algorithms to reason over that data—to find patterns, trends, and anomalies. AI can spot flaws, predict outcomes, and suggest actions. The more the data collected from the system, the better the AI system becomes—as it learns from that data. The industrial metaverse is the meeting ground of information technology and operational technologies—where data from the physical system helps improve the intelligence of the digital system; and the insights from the digital system help improve the efficiency and efficacy of the physical system.
Extended reality
“The consumer metaverse uses VR glasses to transport people into a virtual new online world for entertainment, gaming, and shopping. The industrial metaverse, however, uses AR and MR smart glasses to make digital information and data accessible, which enriches the real world. Through intelligent software running on those smart glasses, the full potential of the industrial metaverse is unleashed. AR and MR solutions, like TeamViewer Frontline, enable digitalised workflows, blueprints, instructions, or holograms to be displayed in the right place and at the right time via the smart glasses—as if they were part of the real environment and without obstructing the workers’ view,” explains Witt. TeamViewer’s latest add-on to Frontline, AiStudio, combines AR and AI. For example, in logistics processes, the AI can be trained to automatically verify if the correct items are picked in the warehouse. It can also be used for compliance checks or quality verification.
Cloud platforms
Software is the fabric that stitches the components of the industrial metaverse together. Microsoft offers a range of tools like Azure Digital Twins, Azure Synapse Analytics, and Microsoft Mesh with Microsoft HoloLens 2 on the cloud. Nvidia’s Omniverse is another popular cloud solution for building an industrial metaverse. Siemens recently announced their new digital business platform Xcelerator. Its solutions are easy to integrate, work together seamlessly, and can be adapted very precisely to specific, individual needs. Last year, Siemens and Nvidia announced a partnership to transform the manufacturing industry with immersive experiences across the lifecycle from design through operation. Companies can use Nvidia Omniverse and Siemens Xcelerator platforms together to enable full-fidelity digital twins and connect software-defined AI systems from edge to cloud.
Here and now
The industrial metaverse is not so far away. Quite a few enterprises around the world have started using the industrial metaverse, or at least its precursor technologies.
“I see three types of use cases to be very prominent in these initial days. First, product demonstrations for sales and marketing events and for customer experience centres. We have already implemented such a use case for a manufacturer of industrial machines. Second, customers want to enhance employee training with respect to complex processes, improve knowledge retention, and simultaneously reduce travel costs. We are presently implementing an immersive learning experience for a client that wants to train its workers in standard operating procedures and simulate specific real-world situations that would be otherwise difficult to replicate safely in classroom training. Finally, there is the digital twin. We have a history of work in this area and now we are starting to create a digital twin of a production line in the industrial metaverse,” says Garg.
“Showcasing products and services in the best possible way is key to the success of any business. To tackle this challenge for a leading manufacturer in the US, we developed a mixed reality solution that creates a true-to-scale 3D hologram of heavy machinery. It allowed digital interaction between the users and the manufacturer while providing a life-like experience,” says Kingsley.
Witt also recalls some of their customer success stories. Food chain Wendy’s uses an AR solution running on smart glasses for livestreaming, staff training, onboarding, and intelligent troubleshooting. This way, they can record deviations in existing processes and suggest next steps for improvement to their employees. They use TeamViewer Frontline, tailored to the hospitality, retail, and food supply chains.
Kemper GmbH, a technology leader for extraction and filter systems in the metalworking industry, uses TeamViewer Frontline for AR based remote support for direct communication in customer service. Experts communicate live with the customers via smart glasses and thus guide them quickly and easily through the problem-solving process.
Airbus Helicopters Inc. uses TeamViewer Frontline in quality assurance and documentation to improve their operations. With the help of smart glasses equipped with a camera and microphone, important data, for example during the maintenance of gearboxes, is documented easily and quickly. Images and voice recordings are uploaded and saved directly in the SAP system via TeamViewer’s solution.
German railway operator Deutsche Bahn’s industrial metaverse, developed using solutions from Nvidia and Siemens, will be based on a digital twin that represents 5,700 stations and tracks covering more than 30,000km. The digital twin will rely on a huge network of sensors working on 5G wireless as well as cameras and lidar detection systems fitted on the trains. The data collected by these devices will be aggregated and used to train their AI system, which in turn will help them understand what is happening, identify problems, and fix them sooner.
In Berlin, Siemens and Bentley Systems are using digital twin technology to create a city district, which will be both 100% CO2-neutral and 100% barrier-free. In London, Thameslink uses Siemens technology to ensure 100% availability of its fleet.
Hellenic, one of Coca Cola’s largest bottlers, serves 29 markets across Europe. It has more than 55 facilities across Europe and produces 90,000 bottles of Coca Cola products per hour on one production line alone. The company has implemented industrial metaverse capabilities with Microsoft to optimise their processes and improve efficiency. According to reports, the factory saved over 9% in energy cost in a 12-week period by building out a sensor fabric, creating digital twins, and allowing factory workers to become immersed in the twins.
Siemens has built a digital native plant in Nanjing, China. The plant’s performance was simulated with a digital twin at the design stage itself. This helped avert planning errors, much before physical construction began. For example, the planning team was able to spot a painting machine without proper ventilation during a virtual inspection. This would have resulted in a lot of trouble in the real-world, but because they detected it in the digital twin in the design phase itself, all it took was a few minutes to change the plan! According to the company, the digital twin has helped the company increase manufacturing capacity by 200% and productivity by 20%.
Anheuser-Bush InBev (AB InBev), the world’s largest brewer with 200 breweries and over 150,000 employees across the globe, is using a private industrial metaverse to transform its operations. They have created a comprehensive digital model of their breweries and supply chain using Azure Digital Twins. The digital model is synchronised with operational and environmental data, to reflect the complex relationships between the natural ingredients and the brewing process. This enables brew masters to adjust settings based on active conditions. Mixed reality overlays help frontline operators to get assistance from remote experts, when required. Deep reinforcement learning helps packing line operators to spot and fix bottlenecks in canning and bottling operations, and schedule maintenance, without much downtime.
Renault Group recently announced the launch of its industrial metaverse, which it describes as a “true replica of the physical world controlled in real time.” All of the group’s production lines are now connected (8,500 pieces of equipment), 90% of supply flows are constantly monitored, and 100% of supply chain data is hosted in the Renault Group Metaverse. The company claims that by 2025, its metaverse will generate savings of Euro 320 million, plus Euro 260 million in inventory savings, a 60% reduction in vehicle delivery time, 50% reduction in the carbon footprint of vehicle manufacturing, and a contribution to the 60% reduction in warranty costs targeted by the whole group.
Kawasaki’s DX initiative uses Microsoft’s industrial metaverse technology to implement a real-time, virtual approach to robot care and maintenance. This technology allows Kawasaki to quickly solve robot failures, and also prevent issues using remote predictive maintenance. The solution can be used collaboratively by customers and partners.
Derick Jose’s tips to progress along the maturity curve of metaverse deployment |
(Source: YourStory) |
Ideal conditions for quick adoption
It is clear that the industrial metaverse can give enterprises a tangible advantage. We asked our experts what kind of infrastructural developments need to happen in the near future to make conditions ripe for mass adoption of the industrial metaverse.
Garg says, “In the next ten years, metaverse would redefine the internet, much like how mobile technology has redefined communication in the past twenty years. Industrial metaverse would help jump-start many industrial companies from the classical e-commerce model to immersive commerce (i-commerce). For this pace of adoption, progress would have to be made on five dimensions. First, the industrial metaverse experience would need to become device independent so that users can connect to the metaverse with the device of their choice—mobile, laptop, headsets like Oculus, and so forth. Second, users must feel safe in the metaverse and hence identity management and robust transaction methodology using blockchain would need to evolve and become standardised. Third, the creation of a community of experts would need to be fast-tracked and proactively built. Fourth, common standards must evolve to allow seamless navigation between different metaverses. Finally, the wide-scale roll-out of 5G network that promises high bandwidth and low latency would enable a high-quality user experience and act as a force multiplier to the metaverse.”
Kingsley adds, “From a mass adoption standpoint, the cost of advanced human-machine interfaces and the compute and energy constraints on devices to derive optimum functionality are some of the significant constraints. However, I envision this improving with better abilities, designs, battery life, and long-term usability in the next three years.”
Nashawaty feels that, “A platform needs to be established for early adoption. Education and buy-in would need to be demonstrated to explain why using the industrial metaverse would be an advantage and also an accelerator to future analysis and product/platform enhancements.”
“While the digital twin is at the heart of the industrial metaverse, it alone won’t suffice to fill the metaverse with life. We not only will need a lot more computing power, faster networks, but also will need more powerful artificial intelligence, better chips, and more advanced virtual reality technologies,” remarks Tutt.
The great Indian opportunity
“We see a lot of startups with capable software engineers launching unique solutions across the board. Apart from this, even the front-end companies offering hardware solutions like sensors or connectivity are expanding their presence in India,” says Siddiqui.
He adds that the official launch of 5G services and massive digital enablement projects will definitely push this space in the country from an adoption perspective.
In his interview with YourStory, Jose said, “For industrial applications of metaverse, it needs a confluence of skills—what Flutura calls the graceful collision of ‘experienced grey-haired folks’ with the ‘young pony tails!’ The experienced grey-haired folks provide domain context to the problem in refining, green energy, process chemicals, and the like. The young pony tails are hungry hackers with limitless energy to find uses for the metaverse and AI to solve real world problems. India is a melting pot of grey-haired folks and pony-tailed folks.” An interesting perspective, indeed!
He explains that India is at the cusp of a renaissance where the country can be No. 1 in industrial AI and industrial metaverse applications, citing examples of startups ranging from Tonbo Imaging and ExactSpace to Flutura and Detect Technologies. Corporations like Tech Mahindra, Wipro, Hexaware, and TCS are also into digital twins and metaverse technologies. As Jose says, “A graceful mix of risk capital, innovative applications, and real-world experience can make the vision of becoming No. 1 a reality through flawless execution.”
Janani G. Vikram is a freelance writer based in Chennai, who loves to write on emerging technologies and Indian culture. She believes in relishing every moment of life, as happy memories are the best savings for the future