Researchers have developed a new method of 3D printing metal structures and multicomponent metal parts at microscale level using hydrogels.
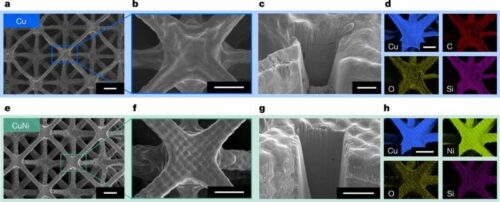
3D printing technology has made designing easier for various industries like education, architecture, manufacturing and even art and jewellery. It allows a person to create structures that are impossible to manufacture by conventional metal-forming methods like forging and inkjet molding, or via subtractive methods such as etching or milling.
Current 3D metal-printing processes use a laser to zap metal powders, which flash melts the metal so it then solidifies into specific shapes. But the problem with these metals, especially those with high thermal conductivity such as copper, is that they transmit heat so well that even with a finely focused laser, heat spreads out and melts powder outside the desired area, lowering the possible resolution of the print.
Researchers from Stanford University have developed a solution to this problem. Instead of writing metals directly, they 3D print a hydrogel and use it as a scaffold for metal-containing liquid precursors. Hydrogels are made from flexible polymer chains which do not dissolve in water. When these hydrogels are exposed to light from low-powered ultraviolet lamps, the polymer chains cross-link resulting in hardening of the hydrogel. If this process is repeated over and over in a specific pattern, desired microscopic shapes can be created.
Researchers then infused the 3D printed hydrogel scaffolds with metal salts dissolved in water (think salty water), causing the metal ions to infiltrate the hydrogel—not just coat its surface. Then, in the “reaction” portion of the process, the researchers burn away the hydrogel portion of the structure in a furnace that reaches 700 to 1100 degrees Celsius, depending on the material. Because the melting point of all metals is higher than the combustion temperature of the hydrogel, the metal remains intact.
The heat removes the hydrogel resulting in shrinking of the overall structure. This process does not only print metals but metal alloys and multicomponent metallic systems, with feature sizes around 40 microns, or less than half the width of a human hair. It has the potential to pave the way for fabricating tiny components for microelectronic mechanical systems (MEMS)—precise components for vehicles and space applications, heat exchangers, or biomedical devices.
References : Max A. Saccone et al, Additive manufacturing of micro-architected metals via hydrogel infusion, Nature (2022). DOI: 10.1038/s41586-022-05433-2