It has been achieved due to improvements in voltage and payload capacity that makes the aerial robots better than their previous versions
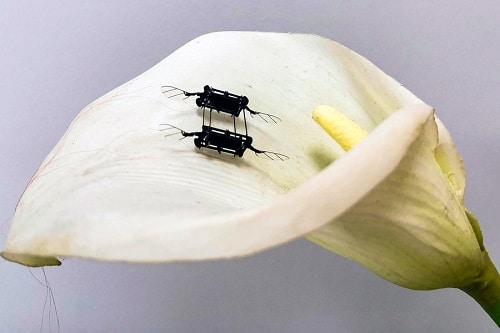
After developing agile and resilient insect-sized drones that manoeuvered like real insects, researchers at MIT heralded a new advancement in micro-drones for use in rescue operations, industrial equipment monitoring or other real-world applications – a feat worth loud applause.
But there was a slight problem: the soft actuator powering the aerial robots required much higher voltages than similarly-sized rigid actuators. On top of that, these lightweight drones didn’t seem to adequately carry the necessary electronics.
So why not resort to rigid actuators and make suitable modifications to them for improved flight?
Well, rigid actuators made from piezoelectric ceramic materials do offer an appropriate flight time, they are, however, quite fragile. Any sudden drop or collision can render the flying ability of these tiny drones useless.
To remove this complication, the MIT researchers tweaked the soft actuators to help the aerial robots accomplish 75 per cent lower voltage and carry 80 per cent more payload than their previous versions – making the actuators act like artificial muscles that rapidly flap the robot’s wings.
Not just that, the latest development resulted in fewer defects and increased the actuator’s power output by more than 300 per cent, thereby extending the robot’s component lifespan for increased performance.
“This opens up a lot of opportunity in the future for us to transition to putting power electronics on the microrobot. People tend to think that soft robots are not as capable as rigid robots. We demonstrate that this robot, weighing less than a gram, flies for the longest time with the smallest error during a hovering flight. The take-home message is that soft robots can exceed the performance of rigid robots,” says Kevin Chen, assistant professor in the Department of Electrical Engineering and Computer Science, and head of the Soft and Micro Robotics Laboratory in the Research Laboratory of Electronics (RLE).
Fabricating the flying robot
Weighing less than one-fourth of a penny, the rectangular microbot has four sets of wings, each driven by a soft actuator made from elastomer layers approximately 10 micrometres thick (about the diameter of a red blood cell).
These layers are sandwiched between two very thin electrodes and rolled into a squishy cylinder.
On applying voltage, the electrodes squeeze the elastomer to produce mechanical strain responsible for flapping the wings.
Optimising the elastomers and electrodes
The research team observed that more surface area of the actuator equalled less required voltage. So several
ultrathin elastomer layers and electrodes were built, which was nonetheless challenging.
“In this process, air comes back into the elastomer and creates a lot of microscopic air bubbles. The diameter of these air bubbles is barely 1 micrometre, so previously we just sort of ignored them. But when you get thinner and thinner layers, the effect of the air bubbles becomes stronger and stronger. That is traditionally why people haven’t been able to make these very thin layers,” Chen explains.
By performing a vacuuming process while the elastomer was still wet after creation, the air bubbles got removed.
For electrodes, carbon nanotubes having diameters about 1/50,000 that of human hair were used. Higher concentrations of carbon nanotubes increased the actuator’s power output and reduced the voltage.
More challenges
The research team encountered more roadblocks than just clearing the air bubbles.
Firstly, if carbon nanotubes were densely packed, then that lead to increased defects. For instance, the sharp-ended carbon nanotubes could pierce an elastomer and cause the device to short out.
Secondly, more elastomer layers made the actuator to become dry less quickly, even taking up to two days, which was time-consuming, especially for adding more layers.
So after a few trials and errors, the researchers decided on an optimal concentration of carbon nanotubes and focused on baking each layer immediately after transferring carbon nanotubes to the elastomer that cut down the previous time.
Final creation
Upon testing the fully completed microbot, it was concluded that the 20-layer actuator (or artificial muscle) required less than 500 volts to operate and had a lift-to-weight ratio of 3.7 to 1 to carry items nearly 3x its weight – a significant improvement from the earlier six-layer version and state-of-the-art, rigid actuators.
Also, the microbot stably hovered in the air for up to 20 seconds, the longest till now by a sub-gram robot.
“Two years ago, we created the most power-dense actuator and it could barely fly. We started to wonder, can soft robots ever compete with rigid robots? We observed one defect after another, so we kept working and we solved one fabrication problem after another, and now the soft actuator’s performance is catching up. They are even a little bit better than the state-of-the-art rigid ones. And there are still several fabrication processes in material science that we don’t understand. So, I am very excited to continue to reduce actuation voltage,” he says.
In future, the research team intends to implement advanced nanofabrication techniques for building insect-sized robots having actuators as thin as 1 micrometre, thus widening the applications of these tiny devices.