Of all the inspections performed during the assembly process, the final inspection is the most crucial as the inspection for finished products will be difficult – especially when involving various angles. With high quality PCBAs expected, comes the need for top-notch inspections. Hence, here is how we address these bottlenecks.
Final assembly inspection is a critical quality control process in the electronic assembly industry that ensures the products (either printed circuit board assemblies (PCBAs) or box build products meet specific standards and specifications before they are shipped to customers. Final Assembly typically consists of Through hole assembly, electromechanical assembly, wire cable assembly and box build assembly and the inspection after the assembly process is relatively important to OQA
The final assembly inspection is a vital step in ensuring the overall quality and reliability of the PCBAs. By identifying and addressing any potential issues before shipping, manufacturers can ensure that their customers receive high-quality products that meet their needs and expectations. Among the possible defects that could be found during the final inspection are label related defects (peel off, printing smearing, damage), cosmetic defects, PCB contamination, damaged components, polarity, wire placement, connector bent pin and flipped components.
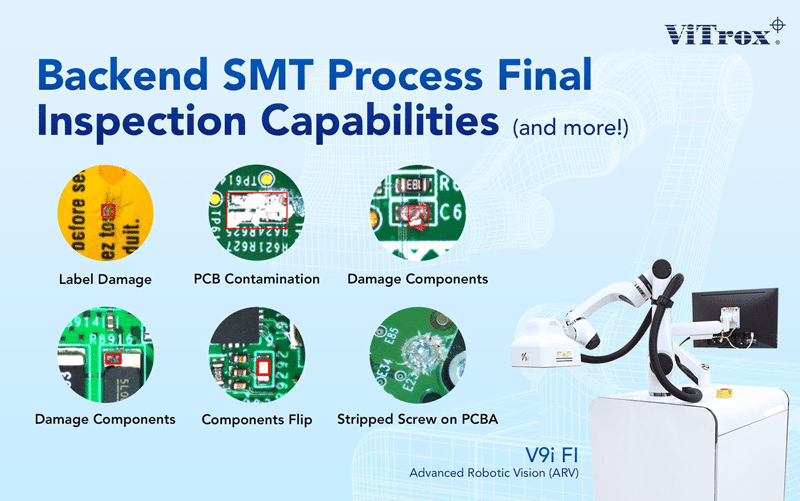
Challenges Posed by Manual Inspection
In the current market, many manufacturers still depend on manual inspection. The reliance on manual labour has many disadvantages, which could also include unnecessary sunk costs.
Firstly, manual inspection will be variable and prone to human error. In order to perfect defect detection, operators need to be trained to spot defects. Typically, the manual inspection is also based on the inspection template to focus on certain inspection regions and might not fully cover the whole board inspection. Not only that, different operators might have different judgements when it comes to assessing defects. Therefore, the quality of inspection cannot be guaranteed, as there are no standard guidelines to achieve consistent inspection results.
Another major disadvantage of manual inspection would be poor traceability, due to a lack of proper documentation, limited data capture, and a lack of automation. Without appropriate documentation, it may be challenging to identify the source of any problems since incomplete or inaccurate records of the parts and materials used may exist. The relevant information, such as the date and time of the inspection or precise batch or lot numbers, may not be captured completely during a manual inspection. This makes it difficult of manufacturers to identify trends that could lead to quality issues or process optimisation.
V9i Advanced Robotic Vision (ARV) Solution:
Where Your PCBA Quality Assurance Is Our Final Goal
On top of the outstanding features that revolutionise conformal coating inspection – highlighted in the previous article, here are the benefits of why our award-winning V9i ARV Solution is a must-have in your production line:
- 2-in-1 Inspection Capabilities To Achieve Cost-Effectiveness
Other than exceptional conformal coating inspection, our V9i ARV also doubles as a final inspection (FI) solution! To equip this capability, our V9i will utilise the Ultraviolet-Red-Green-Blue (UVRGB) module. With this lighting module, the V9i ARV solution can be used for both conformal coating inspection and final inspection. Thus, you will be paying for one solution that covers both your backend inspection processes!
- Comprehensive Inspection Coverage With Highly-Accurate Results
V9i system has the flexibility to offer better coverage on full PCB surface inspection or box build products. The system allows the user to perform top inspection and also side angle inspection on other components, such as USB port connector in case there is any mishandling causing the defect happened. Additionally, the V9i system has multiple advanced algorithms that can program to inspect pin-through hole (PTH), screw quality inspection, wire cable inspection, cosmetic inspection and 5 sided inspection on box build products with the V95i Rotator hardware option!
Other than that, users can perform height measurement with the laser height measurement option that measures up to 100mm components. There are several height measurement modes where users can also set up a simple 3D height measurement. Our V9i ARV solution is built with multi-focal vision, allowing users to adjust the focusing range within 5mm to 200mm, thus resulting in high flexibility on inspection setup with multiple component height. The V9i ARV solution ensures complete inspection coverage and always delivers reliable and consistent results.
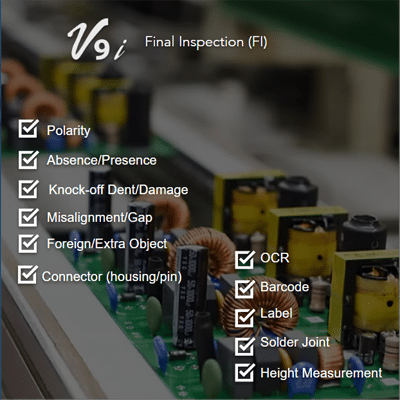
- Reliable Information Connectivity With ViTrox Review Station
Another benefit of our V9i ARV is that the inspection data can be exported and upload to your manufacturing execution system (MES) after the review station buyoff The inspection data and images can be stored in the ViTrox Database Statistical Process Control (VDSPC) 2.0 for future traceability – a critical feature for the Automotive and Aerospace sectors). Users can use barcodes to trace back the inspection data for reference.
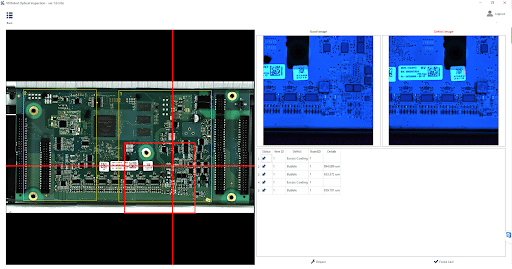
Key Takeaway
Final assembly inspection helps to identify any potential issues or defects that may have occurred during the manufacturing process. The purpose of V9i ARV helps customers to ensure good product quality and reduce the cost by replacing manual inspection in the long run. Most importantly, it is an Industry 4.0-ready solution with real-time monitoring, analysis and preventive actions that guarantee inspection accuracy, consistency, traceability and reliability!