When conceiving and implementing cutting-edge solutions that can thrive in harsh automotive environments a designer would need simulation tools that are interactive, user-friendly, and fast, with minimal hardware requirements. Unleashing power with distributing intelligence imposes real-time feedback on system resilience.
In the automotive industry, designers face the difficult task of addressing, mitigating, and preventing several serious issues that can cause damage to critical components such as the engine control module (ECM) or other electronic control units (ECUs). Malfunctions in these systems can lead to accidents or other safety hazards.
To address these hazards, automotive manufacturers use various protective measures such as fuses, circuit breakers, and overvoltage protection devices, as well as proper thermal management to prevent overheating of critical components.
Accurate simulations can play a crucial role in helping to identify potential issues before they occur, allowing engineers to make necessary design changes and modifications to prevent these issues from happening in the first place.
Additionally, simulations can optimise the design of the electrical system to ensure that it can handle maximum currents and voltages that it is likely to encounter, ensuring safer and more reliable automotive systems.
Ensuring Comprehensive Simulations
In the development of next-generation vehicles, engineers face many challenges in power distribution and need to implement a distributed intelligence approach to simultaneously address the main critical factors:
- resilience;
- efficiency;
- sustainability.
The ability to withstand unforeseen circumstances like accidents, harsh weather, or equipment malfunctions is essential for a vehicle’s resilience. Efficiency plays a critical role in reducing power consumption, emissions, and maintenance expenses while improving overall performance and dependability. Sustainability is a key factor in lessening the impact on the environment and contributing to decarbonisation.
To achieve these goals, engineers must use innovative solutions and concepts that are accurately validated through comprehensive simulations. By doing so, they can develop cutting-edge automotive systems that meet the demands of the industry and provide a safer, more reliable, and more sustainable and enjoyable driving experience.
Intelligent switches for power distribution systems are complex devices that require both electrical and thermal simulations to ensure optimal performance.
Electrical simulations are necessary to analyse the electrical behaviour of the switch, including its ability to handle high voltage and current levels, its response time, and its ability to detect and isolate faults. Thermal simulations, on the other hand, are necessary to analyze the heat generated by the switch during operation, which can affect its performance and reliability. By combining both electrical and thermal simulations, engineers can optimize the design of the intelligent switch to ensure that it meets the required performance specifications while also maintaining safe operating temperatures. Adopting this approach can enhance the efficiency, reliability, and safety of power distribution systems, while ensuring the implementation of adequate and effective protection mechanisms and diagnostics.
Information At A Glance
To ensure the best possible choice, it is essential to conduct simulations in an interactive, user-friendly, and customisable environment that provides a quick understanding of smart switch behaviour. The first step in this process is to determine which products may meet the electrical requirements.
STMicroelectronics’ electro-thermal simulator, TwisterSIM, is an ideal tool for this purpose. It is specifically designed for VIPower products, including smart low-side and high-side drivers and H-bridges for motor control. This simulation tool accurately selects the candidate device from a list, providing a basic information overview.
Therefore, designers can quickly and easily evaluate the performance of different smart switch options and select the best one for their specific application, as shown in Fig. 1.
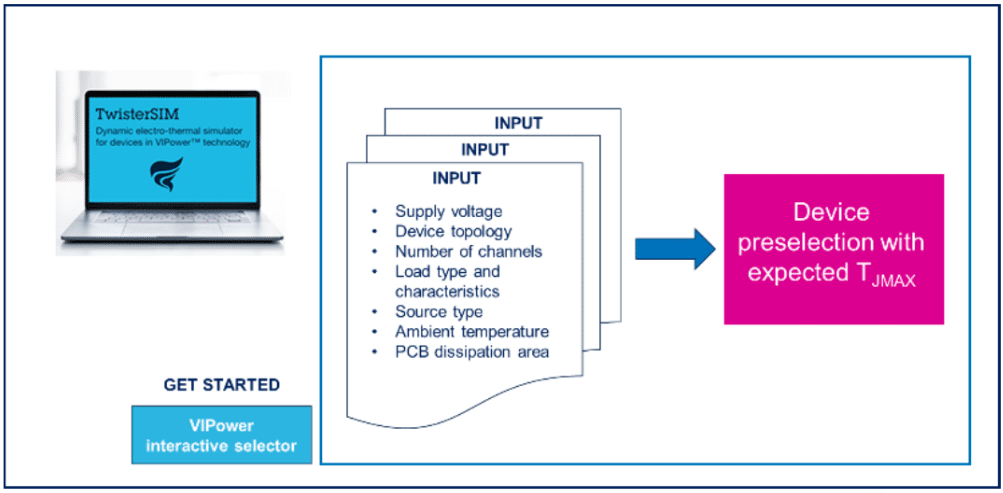
The simulator provides a quick and efficient product preselection by offering valuable information about the expected maximum junction temperature (T JMAX ) based on various inputs, such as supply voltage, device topology, number of channels, load type and characteristics, source type, ambient temperature, and PCB dissipation area.
This information is crucial for selecting the appropriate on-state resistance (R ON ) per channel and ensuring that the thermal budget during operating conditions meets the device’s absolute maximum ratings.
Diving into Performance
To investigate the electrical and thermal behavior of the driver, the simulator generates a schematic circuit that includes the preselected device and input/output connections to the battery and load, respectively (Fig. 2).
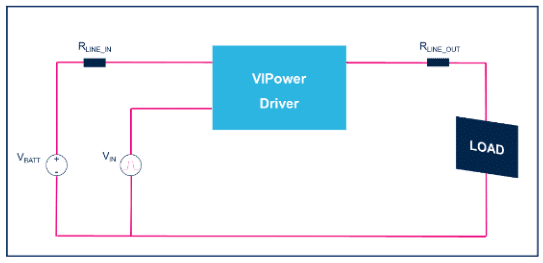
where: VBATT is the battery voltage;
VIN the input voltage provided by the microcontroller;
RLINE_IN and RLINE_OUT the parasitic resistances of wire harness at input and output of the driver.
Before starting the simulation, a definition phase is necessary to customise the project parameters. During this phase, designers define the values of the schematic circuit elements and the simulation setup.
The values of the schematic circuit elements are critical in determining the behaviour of the circuit and must be carefully chosen to ensure that the circuit meets the desired performance specifications.
The simulation setup defines which operative condition the designer wants to reproduce and analyze by means of simulation. For example, the designer may want to inspect the voltage and current waveforms in the circuit, determine the power dissipation, or evaluate the thermal behavior of the circuit.
By customizing the project parameters and setting the simulation variables, designers can ensure that the simulation accurately reflects the behavior of the circuit and provides the necessary information to optimize the design (Fig. 3).
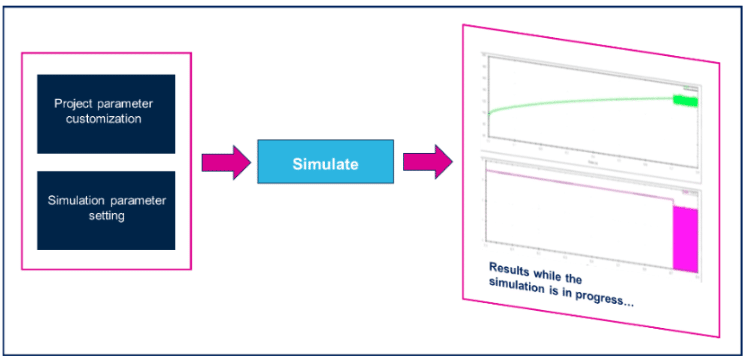
One of the benefits of using TwisterSIM for simulation is that it can display the simulation results in real-time while the simulation is ongoing. This feature allows designers to monitor the behavior of the circuit as it is being simulated and quickly identify any issues or areas for improvement.
The real-time display of simulation results can help designers to optimize the design more efficiently and effectively. For example, if the simulation results show that the circuit is drawing too much current or that the temperature is rising too quickly, the designer can quickly adjust the circuit parameters and immediately see the impact of those changes on the simulation results.
This feature can save time and resources by allowing designers to quickly identify and address issues during the simulation phase, rather than waiting until after the simulation is complete. By using TwisterSIM to display simulation results in real-time, designers can optimize the design more efficiently and effectively, leading to improved efficiency, reliability, and safety of power distribution systems.
Tailoring Results
Engineers can modify simulation parameters, data, and visualization to suit their
specific needs, allowing them to make informed decisions and achieve optima results. The simulator offers a wide range of tools for analyzing and optimizing VIPower circuits, such as thermal mapping, current and voltage waveforms, and power dissipation analysis, as shown in Fig. 4.
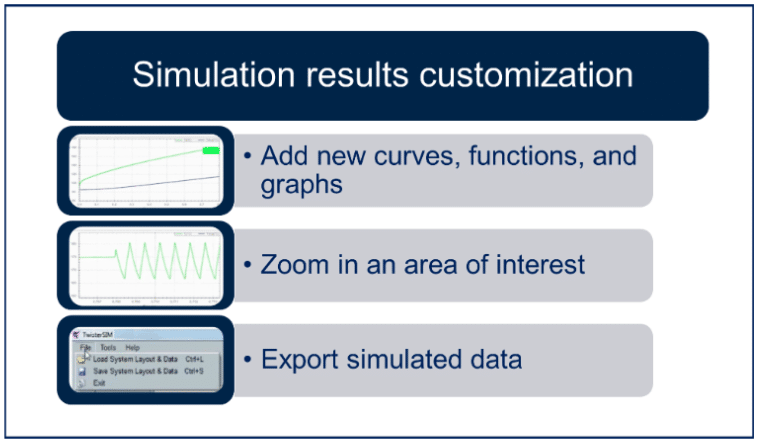
Using TwisterSIM, designers can develop a driver design that is not only efficient but also resilient with effective diagnostics and protections. This is achieved by optimizing the design for maximum performance and reliability, reducing the risk of failure from thermal or electrical stress, and incorporating features such as error replication and limit parameter recording. Additionally, this design approach can sustainably contribute to reducing the vehicle’s CO 2 footprint by reducing wire harness size and weight.
Critical Scenarios
In harsh automotive ecosystems, it is crucial to consider the thermal protection mechanism, especially in situations where repetitive short-circuit events can lead to thermal shutdown (TSD).
In such cases, the driver endeavors to restart the system with a power limitation safeguard (maximum current flow and thermal hysteresis cycling) and remains in TSD mode until the overtemperature issue has been resolved.
This specific control is also implemented in TwisterSim and, considering for instance the high-side driver VND9012AJ, a smart power switch in VIPower M0-9 technology, it can be accurately reproduced. Simulation results can then be compared to experimental data, as shown in Fig. 5.
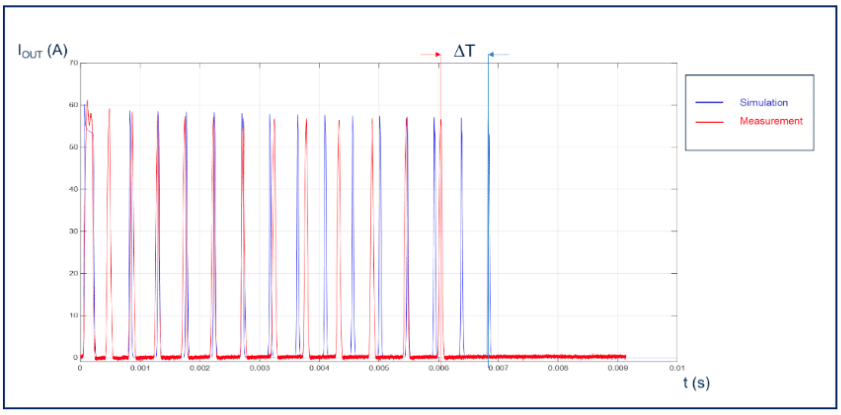
where: IOUT is the output current of the driver;
Δt refers to the time difference between the TSD occurrence in the simulation results and measured data.
The results of the simulation show that TwisterSIM is a highly effective tool for accurately modeling and simulating the thermal protection mechanism in terms of both the current limitation value and the triggering of thermal shutdown (TSD).
The simulated data for the output current value has an error of less than 2%, while the time occurrence for TSD has an error of approximately 0.8 ms. This demonstrates the high level of accuracy that can be achieved with TwisterSIM in predicting the behavior of the system in real-world conditions.
Conclusions
As the automotive industry moves towards the next generation of vehicles, engineers face the challenge of creating advanced solutions that can unleash the power through distributed intelligence. To achieve this, new designs have to prioritize efficiency and resilience, and comprehensive simulation tools are crucial to ensure both accuracy and effectiveness.
By leveraging the capabilities of TwisterSIM, new VIPower driver designs can be
optimized for maximum performance and reliability, while minimizing the risk of failure
from thermal or electrical stress, paving the way for decarbonization and sustainability.
References
[1] “TwisterSIM: Dynamic electro-thermal simulator for VIPower products” Databrief on https://www.st.com/resource/en/data_brief/twistersim.pdf, Sep.
2023.
[2] M. Bonarrigo, G. Gambino, F. Scrimizzi, “Intelligent power switches augment vehicle performance and comfort”, Power Electronics News, Oct. 10, 2023.
[3] A. Brighina, F. Giuffrè, “Interactive analog/digital mixed signal modeling via HDL simulator and foreign VHDL/Verilog C interface”, Electronicsforyou, Electronics & Technology Portal, 2011.
[4] D. Maksimovic, A. M. Stankovic, V. J. Thottuvelil, G. C. Verghese, “Modeling and simulation of power electronic converters”, Proc. of IEEE, vol. 89, no. 6, Jun. 2001.