Silicon carbide (SiC) has a lot of potential to replace silicon in many applications, a significant one being in the automotive industry, especially for battery-operated electric vehicles. To reduce the cost of producing SiC devices, which is quite high, SiC fabs are moving from 15cm (6-inch) to 20cm (8-inch) wafers.
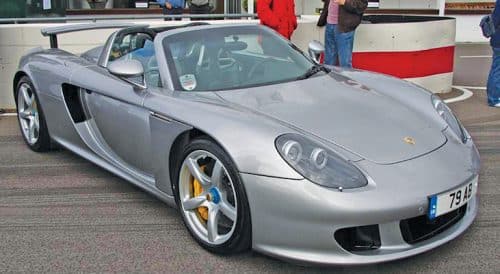
The semiconductor silicon carbide (SiC), commonly known as carborundum, occurs in nature as the mineral moissanite. It is actually abundantly found in space in the form of stardust but occurs very rarely in nature. Nonetheless, since 1893, SiC is being mass-produced for use as an abrasive or in manufacture of light emitting diodes (LEDs) and radio detectors. Today, the ceramics made with SiC, being durable and having high thermal shock resistance, are widely used in automotive brakes and clutches.
Why have we not been using SiC instead of silicon for making semiconductor devices?
Earlier, the main problem with SiC crystals was that they had some defects that prevented them from being used widely in electrical applications. Hence, silicon became the standard. However, with technological advancements in production processes, 15cm SiC wafers are now giving a good yield. Particularly in the automotive industry, using SiC instead of silicon can increase the driving range per charge, speed up charging time, and increase efficiency by delivering the same range with lesser battery capacity and weight.
Importance of SiC in automobiles
Today, the electric vehicle (EV) sector is growing rapidly and governments all over the world are taking initiatives for the preservation of the environment. Moreover, petrol prices and CO2 emissions are a matter of great concern. This is why we can see large-scale investments in EVs. Within the next decade, EVs might very well dominate the vehicle market.
But it is important to note that EVs still cannot compete with conventional vehicles in terms of cost—they are significantly expensive. Hence, EV designers and researchers are looking to increase EV efficiency as that will translate to lower costs. Exploring SiCs has pushed EVs towards this goal.
The very properties that SiC has enable it to be used in devices operating at high temperatures and/or high voltages. Automobiles, especially EVs and hybrid EVs, contain many high-voltage systems like the high-voltage battery and its charging sub-systems.
This makes SiC a good choice for use in such applications. With SiC technology incorporated in MOSFETs and diodes, the whole system can be made smaller, lighter, and more efficient.
Electrical systems in EVs, such as battery management systems (BMS) and onboard chargers (OBC), are crucial since the battery is a fundamental feature of EVs. Typically, the OBC is used to charge the battery using AC mains when the car is parked. This is generally a unidirectional process—from mains to the battery. But OBCs can be used the other way round too, for example, when you want to power your home using the energy stored in your EV battery. By using SiCs in such bidirectional chargers, more efficient bidirectionality can be obtained.
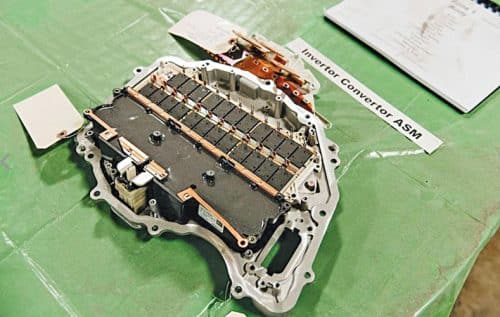
Reasons for the success of SiC
According to BusinessWire, “Global SiC market was valued at US$850.6 million in 2020, and is estimated to reach US$2670.25 million in 2007”. Here are some reasons for its success…
Please register to view this article or log in below.