A sensor-like accelerometer is not something new. It has been miniaturised and volume production has made it so cost-effective that you can put it almost everywhere. Sensor technology started as a component in numerous applications such as mobiles and tablets, but you can now see these in industrial equipment, toys, medical electronics, wearables and even safety in vehicles.
What is driving these little pieces of technology that are so crucial for the Internet of Things (IoT)? Could sensors be the new linen?
The IoT has had a great influence on sensor technology. Whether it is wearables, implantables, smartfabrics or smartpills, improvements in micro-electro-mechanical systems (MEMS) technology and sensors have been one of the driving factors.
Hybrid circuits
Walden C. Rhines, chairman and CEO of Mentor Graphics, told us in an interview that the IoT has created a greater interest in multi-die packaging, in analogue and RF for relatively-low-complexity designs and in hybrid circuits that combine sensors, actuators, MEMS and other things with ASIC chips and then package these accordingly.
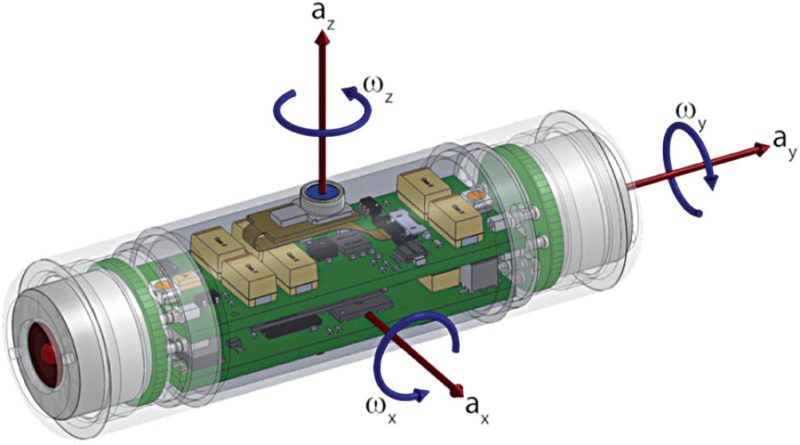
Firms like PragmatIC Printing are developing ultra-thin, low-cost flexible microcircuits that can be incorporated in mass-market packaging. Steven Bagshaw, marketing executive at Centre for Process Innovation Ltd also mentioned how hybrid electronics will give rise to wireless medical devices for rapid diagnostics using printed sensors, thus helping build better medical devices in line with the IoT concept.
Centre for Nano Science and Engineering (CeNSE) at Indian Institute of Science (IISc) is also working on nano-electro-mechanical systems (NEMS). Dr Vijay Mishra, CTO at CeNSE in IISc, has presented a talk on nanotech sensor technology for human body health monitoring at the 4th edition of Electronics Rocks conference that took place in Bengaluru last year.
Scaling up sensor deployment
John Rogers’ materials science research team from University of Illinois, USA, has developed a way of building circuits that act like tattoos, collect power wirelessly and can be worn just about anywhere on the body. Their sensors harvest energy through near field communication to power themselves. Rogers’ company named MC10 Inc. has marketed these in the form of sensor patches, and they are now working on a new generation of the technology since late 2014.
“We have always gone towards higher and higher integration. Starting from small chips, we kept on integrating more features and blocks into it. From just individual sensors in the beginning, we brought in more sensors into the mix to create a sensor hub for engineers. Embedded microcontrollers and a communication system followed this, and the final result is the self-contained unit we see today,” adds Sharma.
Large-area integration of these micro-electronics devices makes the most of their small size by creating processes that can scale these over a larger area.
ISORG and Plastic Logic have a flexible plastic image sensor made from flexible photo detector sensors and organic thin-film technology. This technology won them the prestigious FLEXI award, a recognition given to firms in the flexible and printed electronics segment.
Integrated smart sensors
Newer sensor technology has now integrated vital components of a smart sensor on a chip. It offers a controlled specification set across the operation range of a sensor. The underlying idea here is to integrate sensor technology at the silicon level itself. This is believed to improve power consumption while simplifying product development. How are companies implementing it?
Texas Instruments not only integrates data conversion and communication sections of a smartsensor but also helps in either eliminating the traditional sensing element or integrating it on-chip. For instance, a wheel speed sensor typically employs either a multi-pole ring magnet and hall arrangement or a magnetic rotary encoder and magnet arrangement for measuring wheel speed in vehicles.
“The proposed inductive switch sensor completely does away with a costly multi-pole ring magnet and utilises the metallic wheel hub and printed circuit board itself as a sensor to measure wheel speed. Inductive sensing utilises LC tank resonance to identify presence of metallic teeth and valley as an object to switch between high/low states. Given sensitivity, mounting as well as temperature issues with magnets, new solutions make way for a reliable non-magnet approach and low-cost implementation. Moreover, this technology is enabling the placement of control electronics remotely from location of sensing, thereby making it easier to operate the sub-system away from noise environment,” explains Sanjay Jain, analogue applications manager, MGTS, Texas Instruments India (SC sales and marketing). This technology is also being adapted for a whole lot of other position and speed-sensing applications. It includes passenger-occupancy detection, seatbelt-buckle detection and gear-position detection, to name a few.
Allegro Micro Systems had launched an angle-position sensor that is also programmable. Model A1335 is a contactless, programmable magnetic angle position sensor integrated circuit. It comes with a system-on-chip architecture with a front-end based on circular vertical hall (CVH) technology. It also includes programmable microprocessor based signal processing and supports multiple communication interfaces including inter-integrated circuit, serial peripheral interface and single-edge nibble transmission.
Handling data
Traditional heavy cryptography is difficult to deploy on a typical sensor technology, hence deployment of many insecure IoT devices. “Regulations for the IoT need to address issues of minimum specifications for IoT devices. Existing IoT sensors are not equipped to take advantage of 5G technology either,” explained Kevin Curran, IEEE senior member and reader in computer science at University of Ulster in an interview with EFY.
Production process upgrades
In an interaction earlier this year with Uday Prabhu, general manager, electronics product engineering and product management, Robert Bosch Engineering and Business Solutions Pvt Ltd, he explained that there is compression happening on a large scale with MEMS. An increase in the number of transistors that can go into a chip has resulted in reduced size with higher functionality. Earlier, MEMS elements functioned exclusively as sensing elements.
“Now, intelligence, which is the processor, is built into the MEMS chip itself. This is the primary influencer for the wearables segment, with MEMS chips doubling as control units. Also, structural advances help make finer measurements of acceleration, momentum and so on,” he adds.
Will we soon see the addition of communications technologies to the MEMS chip? Probably not! Prabhu explained that it is good to separate fast- and slow-moving technologies. Otherwise, our wearables would become obsolete very fast and may not support usage with a new, upgraded phone.
What is trending here in Sensor Technology
A lot of applications have long used sensors (of one sort or another) to diagnose, manage and report information. In the last few years, however, sensors have become increasingly important as devices and sub-systems have become more sophisticated with the increase in demand for reliability, especially in safety-critical applications. “The advent of real-time data capture and analysis applications is making these new-age sensor technology increasingly useful in a range of applications including consumer electronics, automotive and in industrial segments,” adds Jain.
Do you want to read more about sensors: click here
Dilin Anand is a senior assistant editor at EFY. He is B.Tech from University of Calicut, currently pursuing MBA from Christ University, Bengaluru
Abhimanyu Rathore is a content specialist at EFY