Everybody uses mobile devices, but how many of us know the secrets of testing for it? We explore the intricacies involved through this interview.
JOT Automation, founded in 1988, develops test and production solutions for smart products, components and electronics. They are a global partner for several industry leading companies including telecom, automotive and life science industries. JOT Automation operates in Europe, Americas and Asia and is a part of Head Invest Group.
Lauri Antila, vice president of Marketing and Business Development, JOT Automation spoke to EFY about the latest in mobile testing and the presence of automation for the same.
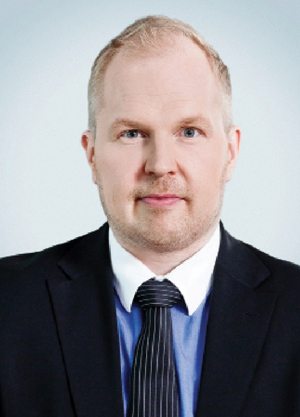
Automation
Q: What are the most important parameters that should be tested in a mobile device?
A. The job starts from the board-level testing, i.e. testing the phones as PCBs and PCB-panels. In addition to electrical testing of the device, we should also take care of software flashing and RF-tuning. In other words, completely integrated and customized test solutions are needed. At this point, the test solutions are often complemented with depaneling and board handling products.
In the final testing phase, we simulate the use of smartphones using a variety of advanced sensor and robot technologies in a repeatable and reliable environment. In practice, our solutions test the proper functionality of microphones, loudspeakers, cameras, radios, dimensions, push buttons, signal lights and displays, touch-screens, and also the testing of all the physical connectors and interfaces, such as USB and audio plug.
Q: What would be an optimal method to test mobile devices, that allows minimum time to market?
A. The best solution would be one that is suitable for a variety of test strategies, processes, end products and applications, which makes them future-proof investments for manufacturers of smart devices. This ensures cost effectiveness for the test equipment. One of the key benefits of such a solution is that the very same test solution can be taken from R&D to production to secure efficient and swift production ramp up. The other key benefit of the solution is the modular system architecture, which enables it to easily adapt to production volume variations during a product’s life cycle, and also between the production lines and factories.
Q: How is the industry going about speeding up the development cycles and overcoming capacity challenges?
A. Modularity and re-configurability is a must here. It is simply not possible to design manufacturing solutions from the scratch for new products. The answer for such needs is platform(s) that can easily be adopted to new product variant or even totally new product. In practice, you need only new test fixtures when changing product in production. This can be achieved in production testing both at board level and product level testing. An example of this is the JOT G3, which enables fully automatic tests on handsets in a repeatable and reliable environment, helping to maximise capacity and quality with low labour costs. Once verified and integrated to a customer’s production testing processes, changing the products to be tested is rather simple. Even test fixtures are based on standard components so basically ramping up new products is about configuring new fixtures.
Q: How do you achieve modularity in your designs? How are you able to provide statistics, traceability and integration to factory systems?
A. We have a long history in modular solutions. Already in the very first business plan for JOT Automation in the late 1980s, the modularity of the solutions was a key thing to achieve. M10 is probably our most advanced solution in terms of modularity. Normally you only change test fixture for new product. To make new kind of test, you would design new test box well. But even in this case, you could use new test boxes in your existing test system including automated handling. M10 functional test solution which consists of Test Boxes, Test Racks, and Test Handlers. They come with integrated test electronics and are available both as RF and non-RF variants, supporting both module and panel-level testing. In a production environment, these Test Boxes can be accommodated to the Test Rack together with third-party test instruments. The Test Rack with Test Boxes can be served manually or automatically with the Test Handler. To create a real test monster, you can have several M10s in a row. Alternatively, for maximum capacity, test phases can be split flexibly, both inside the rack and between the racks. Factory integration is something that can be done by us, customer or by 3rd party.
Q: What is the industry progress vis-a-vis automation of production testing? How will they affect the mobile phone ecosystem?
A. That is an interesting question. I would say that the general development of test systems will give more transparency to the quality of supply chain, which will put brand owners to better position to evaluate the performance of their supply chain between own and contract manufacturing and between the partners and factory network. This will give more flexibility to manufacturing ecosystem. As a simple example, you would use automated solution, instead of operator’s eye, to verify the functionality of the camera zoom. And to get exact automatically generated report about the quality of the process for each step and functionality. In general this will put OEMs to better position.