- Korea Institute of Science and Technology researchers have 3D-printed conductive elastic components.
- The printer ink comprises liquid components dispersed within conductive elastomer material.
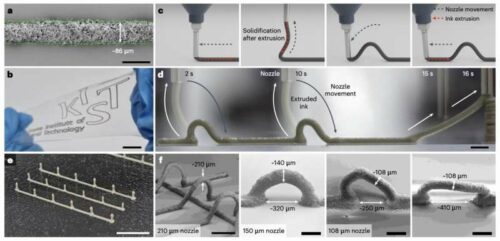
Three-dimensional (3D) printing is now more advanced and can create various items, including electronic components. As the equipment becomes affordable, it could be used to fabricate soft wearable device components. So far, 3D printing has had limited success in producing intricate and flexible electronics, partly due to the challenge of printing solid-state elastic materials that conduct electricity using available inks.
Researchers at the Korea Institute of Science and Technology have used 3D printing to create conductive elastic components. The team have developed a new emulsion-based composite ink for 3D printing flexible conductors. The ink contains liquid components within conductive elastomer material.
An emulsion system consisting of a conductive elastomer composite, immiscible solvent, and emulsifying solvent is suitable for printing elastic conductors in all directions. The viscoelastic properties of the composite support the printed features, enabling the direct writing of freestanding, filamentary, and out-of-plane three-dimensional geometries. The system also features pseudo-plastic and lubrication behaviors, ensuring printing stability and preventing nozzle clogging. The composite ink utilized by scientists possesses advantageous characteristics over other 3D printing inks, notably its viscoelasticity, shear-thinning, and lubricating properties that aid in printing intricate 3D structures.
Printed stretchable conductors have a minimum feature size of under 100 μm and can stretch more than 150%. The emulsion ink’s dispersed solvent phase vaporizes to form microstructured conductive networks on the surface, enhancing electrical conductivity. The researchers printed elastic interconnects and used them to create a wearable temperature sensor with a stretchable display to showcase their 3D printing approach and emulsion-based ink. This method could be used to produce other stretchable and conducting components.
The team believes that combining their 3D printing approach with 3D scanning could result in more comfortable soft electronics. Moreover, the ink’s formulation could lead to new emulsion-based inks with similar properties but different elastomers.
Reference : Byeongmoon Lee et al, Omnidirectional printing of elastic conductors for three-dimensional stretchable electronics, Nature Electronics (2023). DOI: 10.1038/s41928-023-00949-5